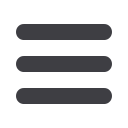

T
ube
B
ending,
H
ydroforming &
E
nd-
Fo
rming
108
M
ay
/J
une
2007
Dynobend, Netherlands, has launched its
latest development: the combi-bending
machine. The complete line of combi-
bending machines consist of the CB12,
CB25, CB40, CB60, CB76 and the CB90.
Equipped with servo drives, this CNC
bending machine combines the advantages
of rolling with variable radii and the popular
mandrel bending technique.
The patented Dynobend bending tools,
which are horizontally divided and vertically
clamped, can be used to bend fixed radii
from approximately 1.2 x D to 3 x D. The
rollers can also be used to roll larger radii.
In combination with the compact bending
head, there is a capability to bend many
different types of products.
All kinds of tools can be used together
with the fixed tools, eg multi-ball mandrel,
wiper die and pressure die. All machines
are equipped with a booster, modem and
network connection. By using the correct
tools, in addition to
tubes it is possible
to bend rectangular
tubes
and
other
profiles. Furthermore,
different types of
materials do not
present a problem.
The machine can
easily be extended
for mass production
by adding a bunker,
loading systems, weld
seam detection, and
unloading
systems.
The bending machine
therefore plays a central role in the production
unit. This enables large savings to be made in
relation to handling and operator costs.
Dynobend BV
– The Netherlands
Fax
: +31 53 8507731
:
info@dynobend.comWebsite
:
www.dynobend.comSpinformed hollow tube
technology replaces
end-cone welding
Formitt Metal Labs, a division of Hess
Industries Inc, offers development,
prototyping and production runs that utilise
patented technologies to form tube ends,
while eliminating welding of end-cones.
The division was created specifically to
support product development for a variety
of industries.
The company uses spinforming, flowforming
and assembly technologies to create hollow
tube symmetrical and asymmetrical shapes,
fabrications, and assemblies. The method
accommodates tubing in both ferrous and
non-ferrous metals, including stainless and
high alloy steels.
By eliminating the need to weld end-cones
to a tube, spinforming technology enhances
overall component quality, reliability and
cost. The company’s hollow tube fabricated
assemblies can include the insertion
of filtration elements, heat exchange
components, catalytic elements, or others.
Formitt metal tube spinforming technologies
are currently being used in the automotive,
HVAC, filtration, marine and other
industries.
Formitt Metal Labs
– USA
Fax
: +1 269 683 1775
Website
:
www.formitt.comHess Industries, Inc
– USA
Fax
: +1 269 683 1775
:
sheffer.rick@hessindustries.comWebsite
:
www.hessindustries.comLatest star in the electronic bending range
Star Bend, Italy, produce electronic bending machines without bending hydraulic
transmission. The range includes thirteen different size configurations, from the simplest
one axis model up to the complete model 6/8 axis CNC, which can bend seven sizes of
tubes from Ø 6x1mm to Ø130x8mm.
This new system, managed
by brushless motors, is
controlled by the latest
generation of digital drivers
and uses the proprietary and
exclusive ‘bending cycles’
management
software
operating in a Windows
environment. This ensures
a line of machines with the
most reliable performance,
purchasing
costs
and
managing costs.
Exclusive
patented
Star
Bend design allows the machine to be entirely modular with the maximum capability
for updates. It is able to interface with any other bending machine, and can interact
with the laser 2 measurement centre laser 2. This interaction is undertaken by remote
workstation or modem with tele assistance.
Star Bend
– Italy
Fax
: +39 030 3583309
:
info@starbend.itWebsite
:
www.starbend.itContinual innovation of mandrel bending
fi
Combining variable radii rolling with mandrel bending – the Dyno CB25
›
The compact bending head fitted to the combi-
bend range
›
Star Bend’s latest bending model, the Star 450 CN6