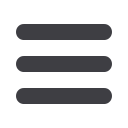

T
ube
B
ending,
H
ydroforming &
E
nd-
Fo
rming
110
M
ay
/J
une
2007
Techniques for manufacturing double wall
tubing have been around for a long time,
yet they are not widely practiced and shops
experienced in the manufacture of double
wall tubing are uncommon. Wolfbend LLC,
USA, is the manufacturer of a patented
lightweight system that enables bending of
tube-within-tube.
Most traditional double wall tube methods
rely on a medium that fills the gap between
tubes to provide support during bending,
which is then removed afterwards.
Commonly used mediums are hot wax,
sand, small metal shot, and metal alloys
such as Cerrobend that melt in boiling
water. The processes for all these materials
are similar.
Hot wax is the most commonly used
method in aerospace. A typical hot wax
process starts with cutting inner and
outer tubes to rough length and applying
corrosion protection such as iridite or
alodine inside and outside both tubes. Long
thin phenolic spacers are cut to size and
epoxied onto the inner tube with a template
to ensure that they are not in bend areas.
After a four-hour cure the inner tube/spacer
assembly is slid into the outer tube and
capped off at one end.
Molten wax is poured into the gap filling 2ft
sections at a time, with a two hour cooling
between pours to allow for contraction.
Bends of 5º or more are X-ray inspected
from 2 directions. The tube assembly is
then uncapped and hung vertically in a hot
water bath or oven for 2½ hours to remove
the wax.
Tubes 6ft and longer are flipped over and
processed a second time. Pressurized
steam is then blown through the assembly
to remove most of the remaining wax. After
degreasing and cleaning, tube ends are
trimmed to length and fittings are installed.
The hot wax method has drawbacks,
primarily due to the characteristics of the
wax. With long tube assemblies, the wax
can cool before reaching the bottom.
Resultant air pockets can lead to lack
of support and bend failures. To help
compensate for this, a minimum working
gap is typically ¼" (ie a 1.00 OD inner tube
requires a 1.50 OD outer).
Bending applies varied forces and wax is
by no means a perfect medium. It behaves
fairly well in compression but tends to
squeeze out which can influence tube
ovality. In tension wax can separate leading
to inadequate support and bend failure.
Proper function also depends on the wax
being completely cooled before bending.
The added weight of the wax usually requires
the bender to be slowed down due to
increased swinging weight and momentum.
100 per cent removal of the wax is very
difficult to achieve and verify, which is a
contamination risk in aerospace applications
such as fuel lines. There are also potential
burn risks in the pouring and removal steps,
particularly when using steam.
Scrap rates can be as high as 50 per cent
depending on material, bend radii, and
complexity of the tube assembly. The
process is slow and labour intensive with
an average two-day processing time. This
can be hard on delivery schedules when
unpredictable scrap rates necessitate
repeated runs.
Wolfbend™ is a relatively new double
wall manufacturing method. It relies on a
bending sleeve that fills the gap between
tubes but remains in place after bending
to support the tubes. For aerospace
applications, where weight is critical, the
sleeve is only used in the bends and
straight sections remain empty. Metallic
grounding spacers are used at both ends of
the assembly to keep tube ends concentric
and provide an electrical bonding path.
A typical Wolfbend process starts with
cutting inner tube rough length, outer tube
final length, and applying iridite or alodine
inside and outside both tubes.
Advances in double wall tube bending
fi
(Below left, middle and right) Cutaways and end view showing the effects of using hot wax as a filler medium for double wall tube bending
(Bottom left, middle and right) Cutaways and end view showing the effects of using the Wolfbend method for double wall tube bending
Bending applies
varied forces and
wax is by no means a
perfect medium. It
tends to squeeze
out which
can influence
tube ovality
❱
❱
88