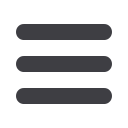

T
ube
B
ending,
H
ydroforming &
E
nd-
Fo
rming
118
M
ay
/J
une
2007
ATE Applicazioni Termo Elettroniche guarantees its Customers
the highest standards of
quality
,
reliability
and
service
in every
stage of a project, from the feasibility study of an application,
through the manufacturing to the commissioning and for the
whole working life of the plant.
All over the world, hundreds of ATE induction systems and
equipments for the heat-treatment of
wires
,
bars
,
pipes
and
straps
prove the reliability of the technical solutions implemented
and Customers’ satisfaction.
Zaniolo CdA-03.07
I N D U C T I O N H E AT I N G T E C H N O L O G Y
A T E N E V E R L E A V E S Y O U
A T A L O O S E E N D
.
ATE A
PPLICAZIONI
T
ERMO
E
LETTRONICHE SRL
Via Soastene 4
36040 Brendola (Vi) Italy
Tel. +39(0)444.601455
Fax +39(0)444.406434
www.ate.it-
info@ate.itATE-Ann. 1/2 07•UK(ok) 26-02-2007 12:13 Pagina 1
AutoForm Hydroforming is a software
solution for the rapid analysis and
simulation of the entire hydroforming
process. It is used by part designers,
process engineers and tool/die makers to
evaluate hydroforming tool designs and
process layouts.
Based on AutoForm’s clear and logical
methodology, the user is guided step-by-
step from the import of CAD geometry until
the generation of the completed tools.
The highly intuitive software provides
handling of single and multiple parts and
automatic cross-sectional part analysis. It
also enables rapid die and process design,
including automatic filleting of sharp
edges, automatic and manual part tipping,
automatic creation of the addendum and
inner fills, and generation of the separation
surface.
Other features include export of complete
surface data, generation of the bending
line, automatic tooling concepts for tryout
simulations, high accuracy of bending and
hydroforming simulations, and fast design
of multiple tooling concepts. Automatic
design and positioning of all required
bending tools and steps can be undertaken
prior to hydroforming. This means that
the time-consuming manual definition of
bending tools and of the bending process
in a CAD system is no longer necessary.
There is also support of complex semi-
finished products such as conical tubes
and profiles, as well as tailor-welded
tubes with varying wall thickness and/or
material properties. These features lead to
improved part quality, increased process
reliability, reduced tooling costs and shorter
development time.
AutoForm Engineering GmbH develops
and markets specialized die face design
and simulation software for the automotive
and sheet metal forming industries.
AutoForm Engineering
Deutschland GmbH
– Germany
Fax
: +49 231 9742 322
:
stefan.werner@autoform.deWebsite
:
www.autuform.comAnalysis and simulation software for hydroforming
›
AutoForm Hydroforming is expert software for
analysis and simulation