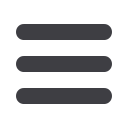

Today’s requirements
Ever-growing cost pressure and
increasingly tougher competition,
internationalization and globalization
affect engineering just like many
other sectors. In the production and
processing industries, these challenges
increasingly throw operating costs
under the spotlight, as machines
are generally operated over decades
rather than just a few years. As
a result, operating costs quickly
outweigh procurement costs: over
an observation period of ten years,
operating costs are often found to be
already five to ten times higher than
investment costs.
Considering costs in their entirety
To achieve a cost-efficient machine,
machine builders and operators should
therefore consider the costs incurred
over the machine life cycle in their
entirety. This approach includes not
just procurement and installation
costs, but also energy costs. Reducing
energy consumption is not just
practical for commercial reasons, but
also for compliance considerations:
legal regulations are increasingly
focusing on this subject. Furthermore,
increasing energy efficiency protects
available environmental resources. In
order to achieve the aim of reducing
energy consumption and increasing
energy efficiency, the energy flows to
the entire machine and the energy
consumption in the individual machine
parts and components should be
recorded, analyzed and then optimized.
An important instrument in this respect
is a systematic power management
system.
Preventing downtimes
Another considerable cost factor in the
life cycle of a machine is the cost of
servicing and maintenance – and in
the worst case, the costs of production
downtimes. As a result, condition
monitoring (or status monitoring) is
becoming increasing important. This
approach can not only ensure the
reliable operation of the machine, but
can also sometimes increase efficiency.
The monitoring is based on recording
the machine status at regular intervals
or on a continual basis by measuring
and analyzing physical parameters
such as motor current, temperature,
fill levels or ambient data. But in
today’s competitive environment, it is
usually no longer enough to simply
react to faults. For just one machine,
the costs of production downtime,
troubleshooting and fault correction
add up quickly. Predictive (or
preventative) maintenance therefore
plays an ever more important role in
Intelligent wiring brings data transparency
to the plant
Heribert Einwag
32 l New-Tech Magazine Europe