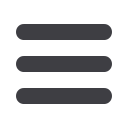

forward it. This means a significantly
upgraded
infrastructure
with
additional components that must
be connected to the control system.
As a result, planning becomes more
complicated, the overall design of
the machine becomes more complex
and the potential for error increases.
Such upgrades also result in a greater
need for input/output modules for the
control system being used – for which
there is not necessarily enough space
reserved in the switch cabinet. If no
smart, communication-enabled variant
is available for ‘simple’ devices, the
machine operator may have to make
a decision between either modernizing
the entire automation system or not
being able to carry out comprehensive
analysis of all machine parts, despite
the high costs associated with this.
An intelligent wiring and
communication system
Technology that offers a solution
to the above challenges must meet
multiple criteria:
Local intelligence for recording and
pre-processing information
Ability to communicate in order to
convey this information
Minimal dimensions in order to be
used even in compact devices such as
pushbuttons or auxiliary switches
Universal applicability thanks to
integration into existing industrial
fieldbus systems
Reasonable price in order to justify
its use even in the simplest switchgear
Smart devices do not require
complex point-to-point wiring, nor
do they need to be connected to
the control system via expensive
fieldbus circuitry. The intelligent wiring
system allows for direct integration
of connected devices to the central
control system or into the machine’s
existing communication environment.
Frequently used pushbuttons as well
as contactors and manual motor
starter or circuit breakers are involved
sensors, switchgears, pushbuttons or
other field equipment.
This level of transparency for a
machine, which goes right to the
sensor, also meets Industry 4.0 criteria.
Machines of the future will consist
of ‘smart’ products that transmit
relevant data, take local decisions,
can establish communication with
other machine assemblies and are
ultimately connected to the Internet of
Things. By exchanging information as
seamlessly as possible between global
production sites on the one hand and
commercial entities and supply chains
on the other, machine operators will
be able to design all their commercial
procedures more efficiently and
operate the machine with maximum
economy. This will provide a clear
advantage in the global competitive
environment.
However, the need for a high-grade
networked machine structure with a
large number of smart, communication-
enabled components must not result
in longer project timeframes. On the
contrary: in a globalized world, time
and cost pressure increases even
during the project design phase. New
machines must be designed, installed
and commissioned within shorter and
shorter timeframes.
Current situation:
expensive wiring and
insufficient depth of data
In today’s machines, automation is
often only implemented in one, but
sometimes multiple programmable
logic controllers (PLCs). These
devices are then connected to motor
starters, variable frequency drives,
soft starters, pushbuttons and modern
control systems installed in the field
or in switch cabinets. All of these
components are usually installed
via industrial fieldbus systems or
complex, expensive point-to-point
control wiring, both of which are prone
to error both during installation and
commissioning and during operation.
Designing and implementing this type
of technology still demands a relatively
high cost both inside and outside of
the switch cabinet.
Data transparency routes
to even the simplest
device
Generally, only the more complex
equipment has its own electronics,
which can be used to record data
and sometimes even pre-process it.
Variable frequency drives and servo
drives, for instance, provide a versatile
range of motor data, can communicate
via virtually every fieldbus system and
often already have externally usable
memory and computing capacity.
In the process they bring with them
all the requirements for high data
transparency of a machine and are
already potentially in a position to
respond as ‘smart components’ within
an Industry 4.0 environment. It is a
different situation with a large number
of components that have previously
been connected via classic control
wiring to digital or analogue inputs/
outputs of the control system in use. In
this case, as well, it would be desirable
to receive more data, but this is often
not possible due to high costs, or is only
possible with a great amount of effort.
For example, if an operator wishes
to process differentiated information
on the reason why a manual motor
starter or circuit breaker has tripped
(overload or short circuit), auxiliary
switches and digital inputs for the
control system must be installed and
wired for each type of data.
More information only available
through additional equipment
To increase availability and reduce
operating costs, machines must be
equipped to offer comprehensive
process monitoring and analysis
options. Additional equipment is
required for this, which can record
or generate the desired data and
34 l New-Tech Magazine Europe