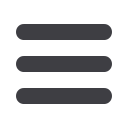

be on call 24 hours a day. This fault
correction procedure often impaired
the productivity of the treatment plant
in the past and incurred significant
personnel costs as well as causing
disruptive downtimes. For this reason,
the company chose to implement the
PKE electronic manual motor starter
from Eaton in combination with
SmartWire-DT.
Thanks to this technology, the
technicians now receive detailed
information on the plant by text
message or email. They can then
interact with the machinery remotely
using a remote connection via virtual
network computing (VNC) and
monitor the current consumption
of each motor in real time, for
example. If the cause of an overload
or a technical fault is determined
and corrected, the drive can be
recommissioned via the touchscreen
of a tablet or smartphone.
Installing this solution has greatly
simplified plant operation for Acque del
Basso Livenza. Today, most problems
can be resolved remotely and the
technicians have time to concentrate
on other tasks. The result: increased
efficiency and productivity.
Modernization – quick
installation and flexible
upgrades
At Germany’s oldest gold and silver
refinery, Heimerle + Meule, a new
automation concept for the refining
process was implemented after a fire.
Six Eaton control units with touch
panels (HMI/PLC) from the XV-102
and XV-152 series were used. These
units communicate via SmartWire-
DT with switchgears such as the PKZ
motor starters, the DIL contactors or
the DS7 soft starter, as well as various
pushbuttons from the RMQ Titan
series. The network comprises a total
of about 300 SmartWire-DT devices.
All HMI/PLCs can be accessed directly
via Ethernet from a central PC.
Amongst other things, a check can
be carried out to determine whether
each connected component is ready
for operation. If an error occurs,
target troubleshooting eliminates the
previous need to search for the cause
of the fault on site.
Thanks to the simple wiring, it took
just three months to modernize the
entire system. Conventional wiring
alone would have taken at least one
month. Thanks to SmartWire-DT,
however, all the components were
installed within just a week. Tedious
troubleshooting was eliminated,
since a large part of the potential
sources of error during installation
and commissioning were prevented
from the start by the plug-and-play
technology of the wiring system.
Using automation components
with an integrated interface to the
intelligent wiring system makes it
possible to reduce the number of
components and interfaces overall
and integrate hardware and software
quickly, effectively and without errors.
Effective wiring – significant time
savings
As part of an extensive new
construction project for a fully
automated potato sorting plant,
Schaltanlagenbau Gormanns GmbH
wired the 250 drives for conveyor
belts, pumps, fans and machines
using the SmartWire-DT technology.
With conventional point-to-point
wiring, an estimated 32 km of cable
would need to be laid for the entire
plant, with at least another 1 km
of cable for traditional cross-wiring
within the switch cabinets.
Today, the control system, variable
frequency drives and touch panels
communicate via a conventional
fieldbus. Motor starter combinations
networked with SmartWire-DT take
over the switching and protection of
all drives. These combinations are
connected to the control system via
one gateway per cabinet and comprise
PKZ manual motor starters, DIL
contactors and electrical connectors
from Eaton’s standard range of
products. The communication system
is not only used in the switch cabinet,
but also with peripheral devices: over
50 command points on the machines
are connected via I/O assemblies with
a high degree of protection (IP65).
The wiring workload was reduced to
one-eighth thanks to the intelligent
wiring system. Cross-wiring dropped
from a good kilometer to just 50
meters and the wiring workload for the
command devices on the machines
was reduced by approximately
40%.
Troubleshooting
during
commissioning also significantly
decreased, as errors were quickly
found using the data supplied by the
connected devices. Instead of two
weeks for commissioning a sorting
plant of a similar age, Gormanns
needed just 1.5 days for the new
plant. The entire complex project was
completed in just four months.
Summary
An intelligent wiring system at device
level makes it possible to equip each
connected component of a machine
with communication capabilities
and decentralized intelligence in an
effective and cost-efficient manner.
As a result, even data from simple
automation components can be
sent to the superordinate control
system or even directly to the local
or supra-regional control level. The
provision of comprehensive data from
the machine leads to a high degree
of data transparency, which can be
used to optimize productivity and
availability. Flexibility, preparation
for the future and ‘IoT readiness’
are additional arguments for using
intelligent wiring systems when
designing or modernizing machines
and systems.
New-Tech Magazine Europe l 37