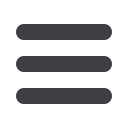

12
Mechanical Technology — November 2015
⎪
Proactive maintenance, lubrication and contamination management
⎪
Mario on maintenance:
T
o wrap up proactive mainte-
nance in 2015, let’s review
what we’ve discussed this year
and delve a little deeper into
some of the aspects that we touched
on, but left for further consideration.
Firstly, let’s remember that each organ-
isation wishing to optimise asset care
must thoughtfully choose between pas-
sive, reactive, preventative, predictive
and proactive maintenance strategies.
We need to do this per asset and/or
major component. Each strategy has a
rightful place in our maintenance mix
and particular set of circumstances. In
deciding, we must consider the relative
importance of reliability against finan-
cial, reputational, safety and environ-
mental matters. We also note that these
are not invariable and, therefore, the
process needs to be repeated at least
every few years as the asset ages and
business circumstances change.
We discussed some of the pitfalls of
the late introduction of predictive main-
tenance into an organisation and con-
cluded that it is a process that must be
handled carefully and that it takes time
as a minimum level of maturity must be
reached. Only then can the full benefits
of proactive maintenance be realised –
by revisiting and adapting preventative
maintenance plans to reduce costs and
enhance reliability. After all, why put
cost into maintaining an asset that has
no need of it and increase the risk of an
infant mortality incident?
It is also useful to be reminded of
the insight into both asset health and
performance afforded by predictive
maintenance techniques. This brings the
potential for useful contributions directly
to the business bottom line by improving
plant performance and efficiency, in ad-
In the final
Mario on maintenance
column for 2015, Mario Kuisis summarises the key
messages for the year, lists some recent technology innovations and warns against straying
from the fundamental rule of physical asset management.
Proactive maintenance:
beyond the starting line
The four pillars of condition monitoring remain vibration and oil analysis, thermography and ultrasound
detection.
dition to reliability. Which, incidentally,
also ticks the right boxes in a number of
environmental and safety aspects.
We mentioned, but did not discuss,
available technology options: scope and
applications; relative ease of use and
cost; method of application; etc. This is
an important topic and worthy of delv-
ing deeper, but very wide ranging and
constantly changing as technological
advances permit improved performance
at lower cost. This is good news for the
new entrant, but also means that if you
want a good and sustained outcome
you must do your homework properly
before investing, then stay abreast of
developments.
The four pillars of condition monitor-
ing remain vibration and oil analysis,
thermography and ultrasound detection.
Do not proceed without first examining
the present state of the art and the merits
of each of these in detail. Incorporate
them as necessary and remember that
they are complementary technologies
with limited overlap. Also bear in mind
that very effective techniques are now
available for monitoring the condition of
many non-rotating assets. If you have
some unusual problems, or want to
explore beyond the conventional, then
listed below are some relatively recent
innovations that are being put to good
use for predictive maintenance by way
of continuous on-line methods.
• Optical fibre as the sensor
for moni-
toring distributed vibration; dis-
tributed acoustics; and distributed
temperature.
• Surface acoustic wave passive wire-
less sensors
for monitoring tempera-
ture; torque; pressure; and strain.
• Gas chromatography
for monitoring
gases, including dissolved gases in oil.
• Conductivity and permittivity
for
monitoring the quality of lubricating
and transformer oils.
• Multi-spectrum structure-borne
acoustics
for monitoring boilers; heat
exchangers; product flow (coal, ore,
etc.); and rotating assets.