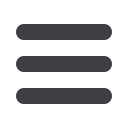

8
Mechanical Technology — November 2015
⎪
Special report
⎪
W
ith roots dating back to
1978 in Calcutta, as a
licensee of the Swedish
company, Skega, Tega
Industries limited is now the flagship
company of the Tega Group of compa-
nies and synonymous with customised
aftermarket products in the mineral
processing, mining, materials handling
and industrial markets.
Founded by the Mohanka family to
provide ‘unique products and services for
handling complex problems in materials
handling and mineral processing indus-
tries’, the company name was changed
to Tega Industries Limited (Tega) in 2002
and it remains a family owned business
with the same philosophy. Tega is cur-
rently the largest non-OEM manufacturer
of a number of moulded wear resistant
rubber components for the mining and
bulk materials handling industries, with
approvals from all major global min-
ing and mineral processing companies
and manufacturing plants across four
continents.
“We are global company active in 72
countries of the world. Wherever there
Customised rubber solutions improve margins
South African production capacity from Tega’s 45 000 m² facility in Vulcania, Brakpan has been increased
by 70% through the addition of 24 new presses.
With the addition of an injection-moulding machine, Tega South Africa can now offer injection
moulded screen panels.
On November 4, wear lining and rubber
products manufacturer, Tega South
Africa, held an open day to showcase
its expanded and consolidated facilities
in Vulcania, Brakpan.
MechTech
attends
and reports.
is mining, we have representation,”
says Syed Yaver Imam, director of global
marketing and product management,
speaking at the company’s South African
open day.
“We have three major manufacturing
facilities in India, along with one here
in South Africa, one in Santiago, Chile
and one in Perth, Australia. We have
sales and marketing facilities in Europe,
Australia, Africa and the Americas,
with a good presence in Latin America
and Canada – and we have offices in
Russia and Uzbekistan, which makes
China the only place were we are not
well represented,” he says, emphasising
that the company is a solution provider
rather than a manufacture and supplier
of standard product.
“Over 500 mills around the world
are now operating using Tega mill liner
technology,” says Imam.
The company established a presence
in South Africa in 2006 with the acqui-
sition of Beruc Equipment. In 2011, it
relocated local operations to its current
45 000 m² property in Vulcania. By
2012, Tega South Africa had won the
contract to supply wear liners for all
ships in the De Beers Marine fleet. The
new plant was officially commissioned in
2013 and by 2014, with the addition of
24 new presses, local production capac-
ity increased by 70%.
The South African facility is ISO
9001:2008 accredited by TUV; has
achieved a B-BBEE equity status of Level
4 and has recently begun to manufacture
injection moulded screen panels. From
the 40 people it took on from Beruc in
2006, Tega South Africa now has over
180 employees.
“We specialise in a wide range of prod-
ucts, with a mining focus that includes
solutions from the run-of-mine side of
operations, through the milling and ma-
terials handling side, all the way through
to extraction and flotation,” continues
Imam, listing chute and hopper linings;
mill liners and lifting bars; screens; and
floatation cells as specialisations.
“In Chile, we have recently com-
pleted an entire optimisation project for
a plant’s piping system, for example.
We increased liner replacement intervals
from two to 12 months. We are also
routinely called to optimise comminution
systems and to improve material flow
via the complete design of the chute
systems so that material can be delivered