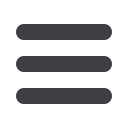

Mechanical Technology — November 2015
11
⎪
Proactive maintenance, lubrication and contamination management
⎪
Above:
The TKSA 51 connects wirelessly to
an associated App, to provide a live 3D view
of the measuring units. Operators can rotate
the virtual machine at their convenience
in all directions, making the alignment as
intuitive as possible.
Left:
The TKSA 51 is a new intuitive App-
powered shaft alignment tool from SKF.
Designed to
suit hazardous
environments, the
SKF Wireless Machine Condition Sensor
provides seamless condition monitoring for
large plants in hard-to-reach locations.
receiving automated commands from
the Wireless Sensor Device Manager
software. This software initiates the
measurement and processing circuits to
take data and transmit it back over the
network. If a node is unable to receive
signals directly from the WirelessHART
gateway, it will, instead, send and receive
its data through a nearby node that can
pass the data to and from the gateway –
forming the mesh network.
Once data is collected, the Wireless
HART gateway communicates with the
Wireless Sensor Device Manager software
supplied by SKF. Device Manager then
automatically exports the data into SKF
@ptitude Analyst where a plant engineer
can analyse the data and determine a
course of action. The Wireless Machine
Condition Sensor has been developed to
be fully compatible with the established
SKF @ptitude Analyst software suite, a
comprehensive diagnostic and analytic
software package.
ATEX Zone 0 certification makes the
product ideally suited for use in hazard-
ous environments typically found in for
example, petrochemical, oil and gas and
pharmaceutical plants.
The unit combines both a sensor
and router node into one compact and
battery-operated unit the size of a typi-
cal industrial accelerometer. The sensor
operates in a low power consumption
mode, allowing the battery to last for
years in the field.
SKF’s Wireless Machine Condition
Sensor offers users a number of im-
portant benefits including an improved
maintenance programme, reduced main-
tenance and installation costs, as well as
enhanced employee and machine safety.
A successful application in
South Africa
Mokse Engineering Enterprises, an
armature winding specialist and one of
SKF South Africa’s key customer, was
so impressed with the capabilities of the
TKSA 11 shaft alignment tool that they
had no hesitation in purchasing the new
TKSA 51 to enable larger machines to
be handled.
Shaft misalignment contributes sig-
nificantly to premature machine failure.
It is estimated that misaligned shafts
can be responsible for up to 50% of
all machine failures. A machine placed
in service with less than optimal shaft
alignment can lead to poor machine per-
formance, increased power consumption,
increased noise and vibration, premature
bearing wear, accelerated deterioration of
gaskets, packing and mechanical seals
as well as higher coupling wear rates.
“These expensive scenarios, which can
all lead to unplanned downtime, costly
repairs and production losses, are easily
preventable using our quality range of
shaft alignment instruments,” notes SKF
maintenance and lubrication product
manager, Eddie Martens.
Mokse Engineering is successfully us-
ing the TKSA 11 for accurate horizontal
shaft alignment of small to medium sized
machines. “It started receiving more and
more requests for larger jobs, but realised
that a tool capable of aligning bigger ma-
chines was required, and because they
were so satisfied with the performance of
the TKSA 11 unit, they approached SKF
for a solution,” Martens relates.
“We demonstrated the TKSA 51 to
Mokse’s engineers, who were immedi-
ately impressed that it could accommo-
date alignment on soft foot (a distortion
in a mounting frame that a motor may
stand on) as well as thermal growth
(caused by thermal expansion),” con-
tinues Martens. “Upon hearing that the
measuring distance between the heads
was 5.0 m, the customer was sold on
the TKSA 51,” he says.
The compact TKSA 51 shaft align-
ment tool provides high measurement
flexibility and performance suitable for
entry-level to expert alignment jobs.
Designed to work with the shaft align-
ment TKSA 51 App on a tablet or smart
phone, this intuitive tool is easy to use
and requires no special training. Martens
adds that SKF can provide basic product
knowledge to an experienced operator as
well as a two day laser alignment training
course on site or in at the SKF training
centre situated in Boksburg, South Africa.
The included accessories of the TKSA
51 makes the instrument ideally suited
for a wide range of alignment applications
such as motors, drives, fans, pumps,
gearboxes, etc. The portable units do not
require installation and are supplied with
a two year warranty.
“Due to the reliable and effective
performance of our TKSA 11 instrument,
we were able to offer the best solution in
the TKSA 51 and assist this longstanding
SKF customer to expand their capabili-
ties by being able to handle larger jobs,
improve turnaround time and grow the
business,” concludes Martens.
SKF is represented in more than
130 countries and has around 15 000
distributor locations worldwide. Annual
sales in 2014 were SEK 70 975-mil-
lion and the company employs 48 593
people.
q