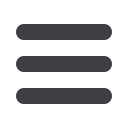

Mechanical Technology — November 2015
13
• Phase angle analysis
of motor voltage and current as an
alternative to accelerometers.
• Wireless hybrid three-axis sensors
for vibration; multi-
spectrum acoustics; and temperature.
Similar developments have been taking place in methods for
periodic on-line assessments. Some interesting examples are:
• Radio frequency detection and analysis
for electrical
discharge current (in bearings, seals, gearboxes, etc.);
partial discharge; and arcing.
• Acoustic stress wave analysis
for condition assessment of
wooden poles (integrity of pole and anchoring).
• Infra-red gas analysis
.
• Ultrasonic detection
for assessing valves; heat exchang-
ers; and steam traps.
The point being made here is that this is a rapidly developing
field and it is quite possible that many unexpected failures,
which would previously have been described as ‘acts of God’
can now be predicted with high levels of confidence – and
not necessarily at high cost, either.
The common thread amongst these is that the technologies
are intended to be used while the asset is in normal service
and without affecting production. This is becoming more and
more important to organisations everywhere, for three main
reasons: to avoid loss of production; in the interests of safety;
and to avoid incidents of repeated infant mortality.
For the purposes of condition monitoring as discussed
here, tests are excluded. In this context a test is understood
to be
a process whereby a stress is imposed on the object
under test and the response to the stress is observed or
measured
. The object may need varying degrees of disas-
sembly but is usually isolated for the test and certainly not
in service. On the other hand, an assessment is passive in
nature by detecting, measuring and analysing signals avail-
able from the object by various means while it is on-line and
in normal service.
This is not to say that tests are not important, just that
they are not an option available to the reliability engineer for
assessing the health of assets in service. Note that here also
technology is making great strides and must be evaluated
when considering shut down inspections.
I would like to finish 2015 with a word of caution.
There is a very real danger that the technophiles in our
ranks (and I admit to being one of them) will become overly
enamoured with the cleverness and intricacies of truly amaz-
ing new technology, cunningly conceived and executed to
solve some real world problems that we think we may have.
However, the risk is that we (or our organisations) do not suffer
from those particular problems. It’s just that we would like to
think they do, so we can have the challenge and enjoyment
of getting our teeth stuck into something new and exciting.
The problem is that unless there are tangible benefits to
the organisation, this will not lead to favourable recognition
and sustained management support, and rightfully so.
Therefore, keep in mind the fundamental rule of physi-
cal asset management, that is: have a clear understanding
of the goals of the organisation and keep every decision in
total alignment with those goals. With that satisfied, taking
advantage of the capabilities of new technology can be both
stimulating and rewarding indeed.
Think of it as unexplored territory to prospect for new
opportunities in 2016.
q
⎪
Proactive maintenance
⎪