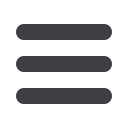

6
Mechanical Technology — November 2015
⎪
Industry forum
⎪
Condition monitoring specialist, Wear-
Check, has set up a comprehensive
network of world-class, full-service
laboratories. One of these sits alongside
its full-service primary laboratory in
Pinetown.
While one of the core functions of the
Pinetown mini-lab is to do preparation
for aircraft filter analysis, it also provides
several other monitoring services and
speciality tests on samples from around
the country, where speciality analysis
is required. Specialty tests conducted
include the analysis of grease, coolant,
Karl Fischer moisture, VPR (varnish
potential rating), and aircraft and
Monitoring service for
reduced distraction risk
Caterpillar has launched of a 24/7 equipment
operator monitoring service to provide custom-
ers the power to see, mitigate and manage the
primary variable impacting their operations – the
human factor. Through industry-leading in-cab
and wearable safety technologies, Caterpillar
can provide customers with visibility to both
machine and operator information.
Inside Caterpillar’s 24/7 Monitoring Centre,
analysts correlate data about the health and
productivity of operators and equipment to re-
veal conditions such as fatigue and distraction
and their impact on operations.
“Our customers want better visibility to the
interaction between operators and machines,
and how behaviour impacts safety and pro-
ductivity,” says Tim Crane, Caterpillar Safety
Services manager. “This innovative solution
offers our customers the opportunity to mitigate
risk and improve productivity. No organisation
is in a better position to provide customers
these sustainable improvement solutions than
Caterpillar,” he believes.
The solutions include Driver Safety System
(DSS™), developed by Seeing Machines, an
alliance partner of Caterpillar; and the wrist-
worn Cat
®
Smartband, an actigraphy solution
powered by Fatigue Science.
www.cat.comFollowing the successful implementation
of a DST Firm Technology Assistance
Package (FTAP), South African compo-
nent manufacture Daliff Precision Engi-
neering has become globally competitive.
The company specialises in complex
machined components for the aerospace,
defence and rail industries.
According to Daliff chairman, Rowland
Chutè, “The installation of Vericut
Software enables us to verify and opti-
DDL Equipment, a leading manufacturer
and supplier of docking systems to South
Africa’s materials handling market, has
new owners. Private equity investment
company, Helikaon Investments, has
taken 100% ownership of the company
and installed a new management team
to increase local sales and expand into
countries abroad.
Helikaon Investments, a majority
black-owned private equity investment
company with wide experience of manu-
facturing and logistics has placed its own
people at DDL’s helm to oversee day-to-
day operations and capital allocation.
DDL is widely recognised as having
driven the development of professional
docking in South Africa. In addition to
locally manufactured dock-levelling and
cold-chain dock sealing systems, it is
the sole authorised distributor for two
leading European door brands, Nergeco
and Alpha.
“We have commissioned a new ERP
system to provide a better overview of
transactions and stock, and enable us to
better communicate stock availability to
the customer base,” Winter says.
WearCheck mini-lab provides maxi service
refrigeration filtration analysis.
The three highly specialised technical
staff members who operate the mini-lab
also conduct field visits to customers in
a variety of industries, such as Illovo,
Tongaat Hulett, Gud filters, and more.
They take samples from gearboxes,
turbines, compressors and any other
component that needs monitoring.
These samples are then processed
and analysed in the mini-lab, and
the results sent to the customer, with
recommendations on what corrective
maintenance action should be taken, if
any is needed.
Trevor Pillay (left, at microscope) is the senior mini-lab
technician, and has been at WearCheck for 26 years.
With him is field and lab technician Shashay Rampersad,
who has clocked up 13 years at WearCheck.
Ten full-service WearCheck laborato-
ries operate across the African continent
and beyond, and are situated in Gauteng,
KwaZulu-Natal and Mpumalanga, with
international laboratories in India, Dubai,
Ghana, Mozambique and Zambia – at
Lumwana mine and Kitwe. WearCheck
also has a presence in Cape Town,
Rustenburg, Steelpoort, Port Elizabeth,
Zimbabwe and Namibia.
An eleventh full-service laboratory is
scheduled to open soon in the Democratic
Republic of Congo (DRC), on-site at the
new Kibali Gold Mine, potentially the
largest gold mine in Africa.
www.wearcheck.co.za“With that in
place, we are now
reorganising and
expanding the ser-
vice department, in-
creasing staff levels
and re-equipping
with new tools, new
vehicles and a stockholding of critical
parts for quicker turnaround times. This
represents a significant expansion and
improvement of the old facility,” he adds.
He points out that increasing electric-
ity costs were forcing cold storage users
to re-examine the efficiency of their en-
vironmental control, and users involved
in maintaining the cold chain would seek
the best possible sealing solutions. “Our
big advantage is that we manufacture our
sealing solutions locally, enabling quicker
installation and a very much quicker
service turnaround times than rival
companies, which import components
from Europe and elsewhere,” says Winter.
“I believe that DDL will enjoy an excit-
ing future, beginning now and continuing
into the longer term,” Winter concludes.
www.ddl.co.zaDDL’s new owners set course for growth
August Winter,
managing director
DDL Equipment.
Local component manufacturer goes global
mise all our CNC programs prior to run-
ning the first article on a CNC machine.
With Vericut, which we would not have
been able to afford without the assistance
of the TLIU, Daliff has been elevated to
a globally competitive level.”
The machine set-up time and ma-
chining cycle time of Daliff Precision
Engineering were both reduced by 20%
as a result of the intervention.
www.daliff.co.za