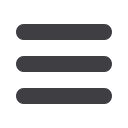

EuroWire – January 2009
51
technical article
Advances in High Speed
Optical Fibre Colouring
By Dr Harri Turunen, Timo Hietaranta, Jukka Mönkkönen, Dr Tim Dougherty, Nextrom (USA) Inc, Conover, North Carolina, USA;
and Nextrom OY, Vantaa, Finland
Abstract
A high speed optical fibre colouring/
upcoat line has been developed to improve
productivity and to provide the flexibility
to manufacture a variety of quality
products. This paper focuses upon the
design of key line components to achieve
speeds up to 3,000m/min for colouring. A
robust mechanical and electrical design,
in combination with optimised tooling,
improved UV lamp system, UV monitoring
instrumentation and increased spool sizes
provide the capability to produce longer
fibre lengths with faster set-ups. The result
is a significant productivity improvement.
1 Introduction
The fibre optic industry is steadily
recovering and is very competitive. This has
generated a renewed interest in process
productivity and the need for equipment
flexibility to manufacture a variety of new
products. During the past few years, the
development of faster curing UV acrylate
resins provided the opportunity for higher
line speeds. In addition, the development
of new fire retardant coatings has led to a
new generation of fibre upcoat products
for premise cable applications
[1] [2]
.
This work focuses upon productivity
improvements for optical fibre colouring/
upcoat equipment. A new machine has
been developed to achieve higher speeds
in combination with longer lengths and
faster set-ups to provide the flexibility
to efficiently manufacture a variety of
products. The new line is shown in
Figure 1
.
It consists of a large capacity spool pay-off
in the lower left, a dancer for pay-off
speed control, a coating station in the
upper centre, followed by a series of high
powered UV lamps below the coater. The
capstan is located in the lower right. The
fibre then passes through a dancer and a
‘tension balancer’, which reduces loops
causing OTDR steps, before being precisely
wound onto a large capacity traversing
take-up spool.
Optional
pay-off/take-up
sizes
are
available, as well as ring marking. Other
options include UV intensity and oxygen
measurements to assure proper UV cure
during long production runs
[3]
.
Colouring trials were conducted on a
prototype line, which is shown in
Figure 2
for
reference. The primary difference between
the prototype and commercial lines was
the relocation of the capstan to the bottom
to make room for optional ring marking
at the top.
2 Critical line
components
The high speed manufacture of coloured
fibres requires improved designs for key
line components. Development focused
upon the pay-off and take-up design to
allow larger and heavier spools, improved
coater tooling to facilitate set-up and fibre
string up, as well as a robust precision
motor drive and control system. New
efficient UV power supplies provide
continuously variable power to the UV
lamps to assure proper cure from start-up
to 3,000m/min.
2.1 Die design
A new colouring applicator was developed
and tested for operation up to 3000m/
min. The challenge was to create the
appropriate pressure inside the coater to
seal the die entrance while maintaining
acceptable fibre tension levels. The line
performance was demonstrated using
DSM Desotech Cablelite® 751 and DX-1000
series inks over a range of operating
parameters.
The results were then compared to
theoretical models. The die tensions, fibre
pay-off or back tensions, and total or maxi-
mum tensions are presented in
Figure 3
for
the average of 751 and DX-1000 colours.
Note that die tensions did not significantly
increase with speeds. This is due to both
shear thinning and shear heating of the
polymer at high speeds. Also note that
the DX-1000 series processed with slightly
higher tensions. This was due to its higher
viscosity as shown in
Figure 4
.
The higher viscosity provides stability
by reducing settling during storage
and between runs. An Arrhenius model
was used to fit viscosity data. Note that
10-15°C higher processing temperatures
for DX-1000 inks would produce viscosities
similar to 751 inks.
Optical grade fibres were coloured during
some of the high speed trials to allow
attenuation measurements at 1,310nm
and 1,550nm. The attenuation increases
were less than 0.01 dB/km at 3,000m/min
for the 751 and DX-1000 inks.
Figure 2
▲
▲
:
Prototype line
Figure 1
▲
▲
:
OFC 52i