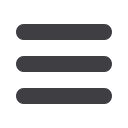

EuroWire – January 2009
53
technical article
Nextrom USA Inc
1230 Commerce ST SW
Conover, NC 28613 USA
Fax
: +1 828 328 4956
:
info.usa@nextrom.comWebsite
:
www.knillusa.comNextrom OY
Vantaa
Finland
Fax
: +358 9 5025 3003
:
info@nextrom.comWebsite
:
www.nextrom.com3 Productivity
The capacity of a colouring line is a function
of many variables including line speed, the
supply and take-up spool capacities, and
the acrylate capacity. The combination of
fibre supply and ink capacity determines
the maximum run length between set-ups.
The maximum fibre length is limited by
the capability of the OTDR to accurately
measure fibre loss to assure that shorter
lengths used in completed cables will
meet final test requirements. The capability
to measure long lengths of single mode
fibre at 1,550nm is over 100km, and at
1,310nm is in the 70 to 80km range. Inks
are typically supplied in 1 or 2kg bottles.
Even a 1kg bottle has more than enough
capacity to colour 100km of fibre.
Other factors affecting productivity include
start-up scrap, set-up times, maintenance
time and operator interference time, which
is a function of line manning.
The impact of these factors upon pro-
ductivity was studied using a model. An
example is shown in
Figure 7
where it is
assumed that the supply length equals the
take-up length. It can also be assumed that
multiple cuts could be made from a given
ink and fibre supply.
Note that as the line speed increases,
the sensitivity to supply spool length
significantly affects line output. This
provides the incentive for longer process
lengths to take full advantage of the speed
capability. For example, a change from
1,500m/min with 25km lengths to 3,000m/
min with 50km lengths would increase the
daily line output from 1,175 fibre km to
2,305km, a 96% increase.
The assumptions include a 55 minute work
hour to account for operator interference,
15 minutes maintenance per shift for
centre tube changes plus any electrical or
mechanical work, 10 minutes per setup,
which includes ink and spool changes plus
string up, a 60 second ramp to 3000m/min
and 10 minute start-up scrap.
To minimise set-up times, clean die
assemblies and new ink containers can
be swapped to allow for offline cleaning
and ink changes. Vacuum is also provided
to the die to minimise ink drip during
shutdown or a fibre break. Both on and
off line automatic die flush systems are
also available. The typical pressurised
ink container holds a 2kg bottle, but
1kg containers are available. Even larger
containers of 10kg and 20kg bottles are
available for fibre upcoat products. Two
options are available for pay-off and
take-ups, the standard 7kg spool (ie 50km
of fibre) and a larger 25kg supply for
upcoated products.
4 Conclusions
The result of the key line component
improvements is a new high speed
colouring/upcoat line with the potential
for speeds up to 3,000m/min.
The line includes a new coating applicator
and more efficient UV curing system with
inert atmosphere controls. Also included
is a greater range of pay-off and take-up
sizes and a robust responsive drive system.
These essential components of the process
were proven to perform via extensive
testing and curing level measurements.
Previous developments of UV upcoating
and ring marking were incorporated
into the new design to provide the
flexibility to manufacture a wide variety
of products.
n
5 Acknowledgements
The authors wish to thank many co-
workers at Nextrom and Keqi Gan and
others at DSM Desotech for their assistance
with the colouring trials plus the RAU and
the MEK rub measurements.
6 References
[1]
Tim Dougherty, Harri Turunen, Jari Nykänen,
‘Buffered
Optical
Fibre
Manufacturing
Developments’, Proceedings of the 52
nd
IWCS/
Focus, 616-622 (2003).
[2]
Eva Montgomery, Ed Murphy, Keqi Gan, Ken
Drake, Nathan Drake, ‘UV-Curable Buffer Resins
vs Thermoplastics: A Closer Look at New Flame
Retardant, UV-Curable Materials in Tight Buffered
Cables’, Proceedings of the 52
nd
IWCS/Focus,
98-101 (2003).
[3]
Rick Chamberlain, Paul Schmugge, Bob Stulpin,
Harri Turunen, Tim Dougherty, ‘Optimisation
of UV-Curing Multiple Elements by On-Line
Measurements’, Proceedings of the 54
th
IWCS/
Focus, 83-88 (2005).
[4]
Harri Turunen, Tim Dougherty, Jari Nykänen,
Eva Montgomery, Keqi Gan, ‘The Manufacture
of UV-Curable Buffered Optical Fibers’, China
International Wire and Cable Conference
(Non-Ferrous) Wire China 22
nd
-23
rd
September,
94-103 (2004).
Figure 7
▲
▲
:
Line output/day