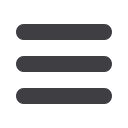

EuroWire – January 2009
52
technical article
To allow optimisation of the internal die
dimensions, a one dimensional die flow
model was created. The model assumes
Newtonian flow at any given cross-section,
but allows the viscosity to vary with the
average shear rate at that section.
A Carreau-Yasuda model in combination
with an Arrhenius equation was utilised to
define viscosity as a function of tempera-
ture and shear rate. The fibre tension
and the pressure within the die are then
calculated as illustrated in
Figure 5
for a
given coloured fibre diameter, line speed
and temperature.
Note the extra tension build-up within
the exit die as the fibre accelerates the
acrylate creating high pressure, which
provides centering forces to assure a
uniform coating. The manifold length was
shorter than used in fibre coating, but
longer than used in a typical colouring die
to enhance ink recirculation, temperature
uniformity and to create moderate fibre
tension at high speeds.
The maximum 1.7 N tension at 3,000m/min
only exposes the fibre to 0.14 GPa [20 kpsi]
stress, which is 20% of typical 0.69 GPa
[100 kpsi] proof test levels. This moderate
tension minimises the amplitude of fibre
vibrations within the UV lamp system. The
simple design also facilitates die cleaning
and string-up.
2.2 UV curing
Development focused upon
inert atmosphere control and
the tracking of an efficient
powerful UV curing lamp
system. The new Fusion UV
Systems Light Hammer® 10
electronic
power
supplies
provide continuously variable
DC power from 35% to 100%.
The
result
is
improved
magnetron and lamp life plus
significantly reduced power
supply weight to facilitate
maintenance. Instrumentation
is provided to measure the
nitrogen flow rate, the oxygen level,
and the UV intensity through the centre
tube to signal the need for centre tube
changes to assure proper cure. At 3,000m/
min, three 10 inch long 600 W/inch lamps
were used with type D lamps to provide
excellent depth of cure. Optionally, an
H bulb can be substituted for one D
bulb to improve surface cure. The use
of 3 separate lamps also allows a 10 to
1 range in UV power level during ramp up
to match the required UV dose with speed.
A single centre tube is inserted from above
through all 3 UV lamps, which are mounted
together on a slide that moves outwards to
facilitate tube changes.
The UV design was verified via extensive
testing and curing level measurements
using the DSM 751 and DX-1000 series inks.
FTIR cure measurements were provided by
DSM Desotech Inc for samples that were
made over a range of speeds using two or
three 600W/Inch Fusion lamps at full
power. The Percent Reacted Acrylate
Unsaturation (ie % RAU) results presented
in
Figure 6
are an average of several colours,
because the ±3% accuracy of individual
readings. These results demonstrate the
high-speed capability of the acrylate
coating-curing process.
The UV cure is a function of the relative
UV dose, which in turn is a function of the
lamp power levels, the number of lamps
and the line speed.
The relative dose per unit
length was calculated by first
multiplying the lamp power per
unit length in each lamp by the
corresponding residence time
in that lamp. Then the doses per
unit length were summed over
the lamps in the system. The
actual dose is significantly lower
and is a function of the overall
UV power conversion efficiency
plus the size and distribution
of the energy within the lamp
sweet spot.
For an equivalent UV dose,
the DX-1000 series had the
highest cure. The 751 inks had cure levels
above 84% for ribbon applications up to
2,500m/min. The DX series had excellent
cure at 3,000m/min with either two or
three lamps, thus demonstrating its faster
cure performance. In addition, DSM also
performed MEK double rub tests to check
actual ink cure performance. All samples
survived more than 200 rubs, even when
the RAU was 80%, again demonstrating
excellent cures.
In summary, a maximum colouring speed of
3,000m/min was achieved, while as reported
in previous trials
[4]
, the maximum 0.9mm
up-coat product speed was 900m/min.
2.3 Line drives
To improve the responsiveness and
accuracy of critical motors at high speeds,
a separate motion controller is used to
control the capstan, the dancer-spool
rotation loops and the traverse motor,
which controls the winding pitch and
spool reversals. A PLC provides overall
line coordination via Siemens Profibus or
Allen-Bradley DeviceNet™ for the motion
controller, the UV lamp system, the coater
and other components. The result is a 10 to
1 improvement in control response times,
which is critical during rapid ramps and to
assure precise fibre winding. In addition,
an automatic turning point correction
is provided at reel flanges. An algorithm
varies both pitch and reversal points to
assure level winding.
Figure 3
▲
▲
:
Coloring tension vs speed
Figure 4
▲
▲
:
Comparison of ink viscosities
Figure 5
▼
▼
:
Die characteristics
Figure 6
▼
▼
:
Percent cure via FTIR vs relative dose