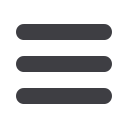

news
Wire & Cable ASIA – September/October 2008
52
The AVS, automatic winding width control, from Joachim
Uhing KG GmbH is a system to prevent the formation of dents
and bulges in the switchover area during spool winding, to
ensure high speed unwinding during post-processing.
“The formation of dents is particularly critical during winding,”
explains Burkhard W Bohn, managing director of Uhing’s
technology sector. “Dents bear the risk of slippage, followed
by bulging layers being wound on top. During unwinding, this
can cause jolts and result in material rupture.”
AVS detects even the first signs of dents and bulges during
winding. The intelligent device memorises the respective
position and corrects the error during the next strokes. This
results in the spool being completely filled with a continuously
cylindrical winding.
Correction occurs in respectively defined windows before the
switchover points by changing the winding width. The stroke
increases
at
this
end when a dent is
detected. During the
next strokes more
material is fed, and the
dent is filled. In case of
a bulge, the stroke
decreases accordingly,
and less material is
fed. “These corrections
are based on the
requirement that line
speed
and
spool
speed is proportional,”
explains Bohn.
“Sensors monitor both
values. The AVS inter-
prets an increase of
the spool speed at
constant material speed as a dent since the winding diameter
must be smaller at the deviation point.
“On the other hand, the AVS interprets a decreasing spool
speed as a bulge.” The AVS will immediately react by
compensating the error on the respective side.
The controller is suited for all winding systems that use
electrical pulses to switch over. It can handle cylindrical and
bi-conical spools as well as conical winding on cylindrical
spool cores.
The AVS can be implemented for Uhing rolling ring drives and
other winding systems such as timing belt or threaded spindle
drives. Existing winding systems can be retrofitted.
“The AVS can store up to ten different spool types,” says
Wolfgang Weber of Uhing Marketing. “An optimum winding
result can be achieved automatically, even in dirt-laden
environments.”
Joachim Uhing KG GmbH & Co – Germany
Fax
: +49 4347 906 40
:
weber@uhing.comWebsite
:
www.uhing.comUhing unwinds at
high speed
F
I
N
I
S
H
E
D
F
O
R
P
R
E
C
I
S
I
O
N
Programme:
tc. Drawing dies / Casings
➘
Die working machines
➘
Spare parts
➘
Service & Technical assistance
➘
Diamond suspension
➘
Diamond grinding pins
➘
Calibration pins L=80 mm
➘
Calibration wires L=35/40 mm
➘
Conical steel needles
➘
Machines
Die cone polishing machines for small
diameter (steel cord) Ø 0.15 – 2.00 mm
The die working machines KPS1 & EK2000F
are equipped with a Siemens Simatic SPS
Control and therefore offer a high degree of
automation and efficiency. The die geometry
as well as well as the diameter can be
determined without any need of skilled and
experienced operators.
Calibration pins
We dispose of a new CNC-controlled High Tec machine,
for the production of high quality Calibrating pins,
particularly to be able to produce these pins
also in graduation steps of 0,001 mm,
with an accurate tolerance of 1 μm.
To assure the accuracy of these very small tolerances,
we dispose of a laser analyzer, where all Calibrating
pins are verified after and during the production,
to guarantee a very high preciseness of all pins
manufactured by this new machine.
WIRE Shanghai, 23.09. – 26.09.2008
F25 Hall W1
Drawing dies & modern Tc. Die working equipment
Im Seifen 18 / D-35756 Mittenaar
(
++49 (0) 2778-2281 /
++49 (0) 2778-2190
www.bremer-willi.de Bremer.Willi@t-online.deJoachim Uhing KG GmbH & Co
m
m
launches the AVS, automatic winding
width control system