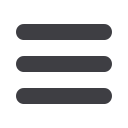
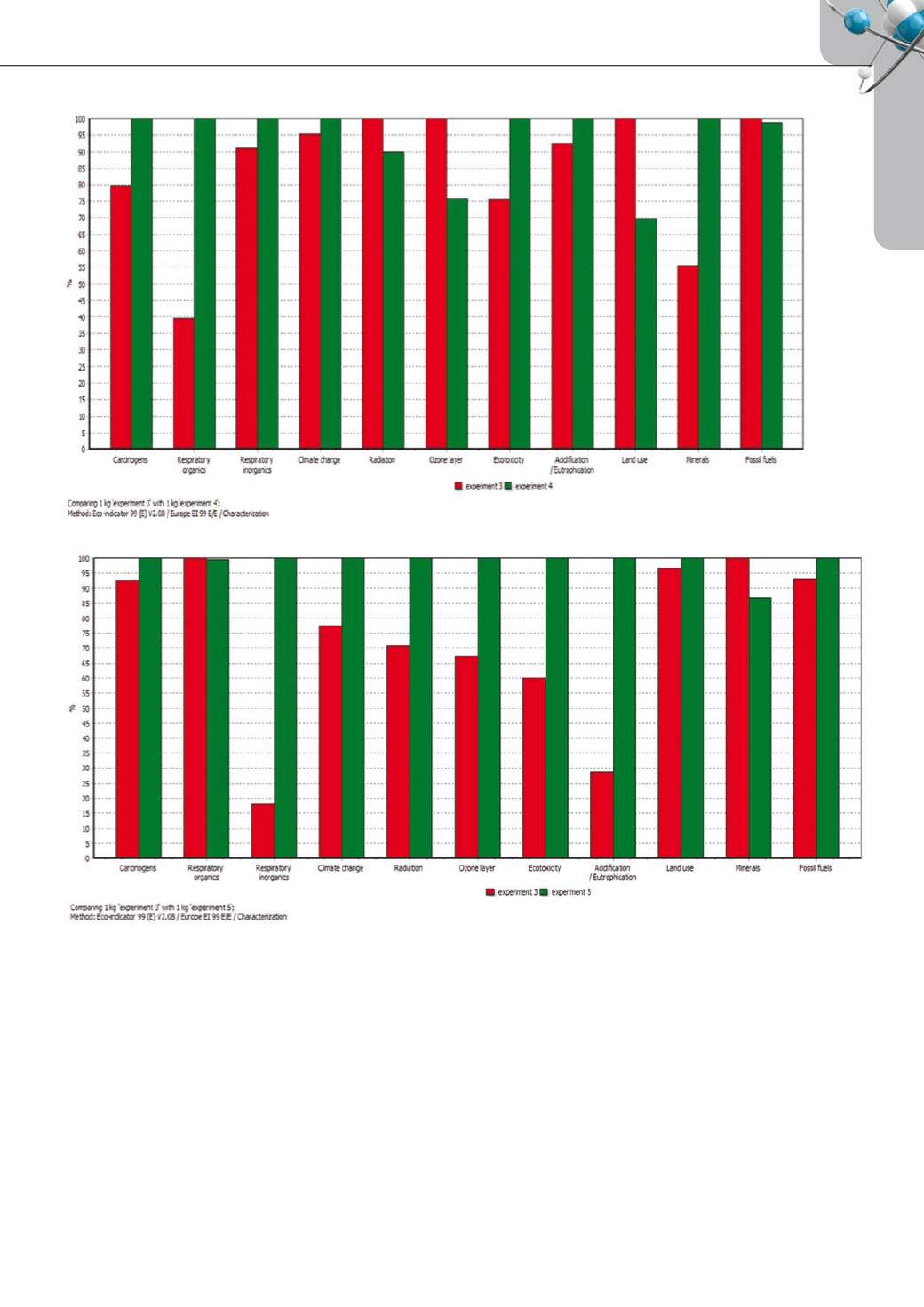
9
Petrochemicals
Chemical Technology • February 2015
400 ml of waste cooking oil was used, however, the volume
of alcohol used varied from experiment to experiment. The
chosen system boundary included the production process
(experiment), assembly, transportation to the selling point
and burning of biodiesel in an engine, however, the initial
process of growing and harvesting the oil crop was excluded
because the use of waste cooking oil for the production of
biodiesel is considered a waste treatment process. The
system boundary remained when performing Life Cycle As-
sessments for different biodiesel production routes in order
to obtain a good comparison.
The conducted lab scale experiments were not continuous
(batch process) and the alcohol was not recovered from the
process; it was assumed that 94% of the unreacted alcohol
will evaporate and the remaining is washed out with other
impurities during the washing process. The Life Cycle Assess-
ment (LCA) was performed on a mass ratio allocation basis
because of the useful by-product glycerol that is obtained
during the experiments.
ECO-Indicator 99 gave back the contribution of the dif-
ferent biodiesel production routes in 11 impact categories
namely eutrophication/acidification, climate change, carcino-
gens, respiratory organics, respiratory inorganics, ecotoxicity,
radiation, land use, minerals, fossil fuels and depletion of the
ozone layer. The transportation distance of 5 kmwas chosen
on the basis that the production facility will be placed nearby
selling points in order to reduce the environmental impact of
the transportation of biodiesel.
Figure 1: Impact assessment results using
the Eco-indicator 99 (E) V2.08 method/
characterisation- comparing methanol to
ethanol using KOH as a catalyst
Figure 2: Impact assessment results - comparison between the
catalysts, KOH and NaOH, using methanol, Eco-indicator 99 (E)
V2.08/ Europe EI 99 E/E method/ characterisation
WASTE MANAGEMENT