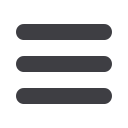

12
Chemical Technology • February 2015
J
ust as stress can accelerate deterioration of metals
in a corrosive environment, operational stress moves
equipment and systems toward failure. Limiting stresses
within the operating environment maintains reliability.
The elements of the maintenance which are relevant are:
1. Protecting components from stress
2. Monitoring their condition, and
3. Undertaking component(s) replacement prior to the
failure threshold level caused by stress excesses.
The impact of maintenance costs over time spans which
can easily reach 25 years or more is finally much higher
than savings made on the investment side when purchasing
inappropriate valve technology, or when choosing solutions
not being ‘state of the art’ technology. The aim of this article
is to show, using the example of industrial
(butterfly) valves, how quality of components
is effectively influencing the cost efficiency
of industrial production plants.
Asageneralrulevalvescontribute1%–3 %
of the total investment costs of industrial pro-
duction plants. Therefore valves often suffer
from a certain lack of consideration, even
though, in the worst case scenario, one valve
failing can lead to a plant shut-down. Hence
it is important, from the beginning, to choose
the most suitable flow control technology.
This commences with the choice of the ad-
equate valve type, and the definition of the
appropriate valvematerials to be used. Once the valves have
been installed, and the plant put into service, operational
and maintenance costs start running. Quality aspects of the
valve have a considerable impact on operational cost, as, for
instance, on pumping capacity, power demand of actuators,
and energy efficiency of the entire plant.
Corrosion is one of the major threads in industrial pro-
cesses, having an important influence on cost aspects.
Therefore it is important to design the valves by using innova-
tivematerials and adapted solutions in order to prevent such
corrosion damages and thus additional costs.
The expectations for a production plant are evident:
safety to the employees and the environment, constantly
high product quality and plant as possible and operating and
maintenance costs as low as feasible.
Finally the dilemma often lies somewhere between
aspects of CAPEX and OPEX. As an example, when using
components with a low average material lifetime (AMLT),
savings on the CAPEX side can be made, but, on the other
hand, OPEX will be higher because they are replaced more
frequently. On the other hand, attempts to reduce specific
costs of maintenance or repair, most often end in higher
CAPEX. Consequently, using high end components and ad-
vanced technology will provide a safer operation of the plant,
higher production quality and a more favourable total cost
of operation (TCO).
One to three percent of the investments costs of an indus-
trial plant are caused by low and medium pressure valves,
while maintenance costs including replacement and repair
of such valves are estimated to be in the range of 4 – 7 %
of the OPEX.
Lifetime expectation of valves used in production pro-
cesses generally is in the range of 5–10 years, depending on
the quality of the valve, the working conditions, the frequency
of operation and quality of maintenance. A standard quality
valve is expected to provide ten years of trouble-free service in
these applications. Speciality valves can give reliable service
for time spans of 15 or more years. In extreme cases, valves
only last about two weeks, and quite often valves have to be
replaced after three to six months. In such cases it is mainly
corrosion, abrasion and scaling that are the cause of these
very short lifetimes. Themain effects are internal and external
leaking, with all the consequent effects.
When looking at butterfly valves, for example, various
aspects affect the lifetime expectation (AMLT). One of the
most important sources of valvemalfunctioning results from
the design and quality of the sealing elements. The lifespan
and reliability of elastomeric seated butterfly valves is largely
dependent on the valve liner which is the heart of the valve.
Careful evaluation of this seemingly simple element should
Big effect on small cause –
Valve technology under stress
Maintenance can be defined as the
degradation management of engineered
materials (equipment and systems) to
retain their performance within their
designed operating parameters.