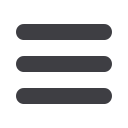

14
Chemical Technology • February 2015
Equipment failure prevention needs defect elimination strategyA
ll equipment starts life new. It comes from the
manufacturer fresh. If you do nothing about control-
ling it, it also comes with future failures built into it.
These future failures are the design errors, the materi-
als selection errors, the fabrication errors, the assembly
errors and any transportation damage. When installed,
further causes of future failures arise from incorrect
installation, incorrect site assembly, incorrect mount-
ing practices, inadequate environmental protection and
deficient foundations/supports.
Some of these errors, along with commissioning
errors and operating errors, cause failures early in the
equipment’s operating life and explain early-life or ‘in-
fant mortality’ failures. Those defects and errors that do
not appear during equipment infant-life, will eventually
surface and cause failures sometime later, during its
operating life.
The preferred terminology is to call the errors ‘defects’,
because that is what you see as a consequence of the
mistake. But the truth is that a wrong action (or no action)
was taken at some point in time and as a consequence
a defect resulted.
Another truth is that most times, most things go right.
Failure is not the normal situation. The problemwith failures
is not the failure in itself. It is the consequences resulting
from them. When the consequences of failure are bad, you
want to do everything possible to never again let them
happen!
Defect elimination is the answer
Starting fromnew, a part properly built and installed, without
any errors, will operate at a particular level of performance.
If looked after properly it should, ideally, deliver its design
requirements all its operating life.
As its operating life progresses, any of those previously
hidden manufacturer’s and installer’s errors noted above
start to make their effects known. For some reason the
equipment starts to fail. Failure causes can be introduced
at any time. They can appear during operation frommanage-
ment decision errors, operating errors, repair errors, abuse
and even acts of Mother Nature.
If you want superbly reliable equipment you must prevent the
introduction of defects and errors at all stages of the equipment
life cycle, and also act to remove the defects and errors already
present in it.
By getting rid of the defects that generate future
failures, you will greatly reduce your future maintenance
requirements, and hence guarantee great production
performance.
An average item of equipment has several dozen direct
and consequential failure modes. The best maintenance
by Mike Sondalini, Managing Director, Lifetime Reliability Solutions, Lean Manufacturing,
Enterprise Asset Maintenance and Work Quality Management Consultant Services
To reduce maintenance costs and
production downtime it is necessary to
reduce their causes. Both are effects and
not causes which can be traced back to
defects and errors: defects lead to future
equipment failures, production downtime
and lost profits. Thus strategies prevent
their occurrence and eliminate them if
they do occur.