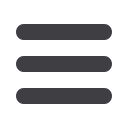

5
Disclaimer:
The content in this paper is loosely based on experiences, and have been embellished to bring out the salient points
against the objectives of this paper.
If the HAZARD is toxic gas such as H
2
S and the concentration in the process stream is high, then even
small releases may have severe consequences.
If release is liquid and non-toxic or hazardous (e.g. water), then smaller releases may be acceptable and
only significant leak rates that trip or upset the process are to be considered for detection.
If the release is liquid and hydrocarbon, then what release size could be tolerated before leading to a
hazardous event? This should be analysed, and maybe even modelled, to determine acceptable limits.
If the release is flammable gas, then what events would low pressure detect? For a pipeline even a
catastrophic release close to the feed source may not be detected by low pressure detection located at
the feed source.
Low pressure detection may have a role to play in process safety, but each application should be based
on the hazard and the ability to detect the hazard.
Standards that provide guidance that is towards prescriptive methods may miss the real hazard, and as
such may give the end user a false sense of safety.
The summary of this case study is that:
1.
Know your hazard, and always carry out Hazard and Risk assessment.
2.
When leak detection is required the allocation of the safety function should consider:
a.
the best detection method
b.
the detection time, and
c.
the response action
3.
Use Standards wisely. Do not always blindly follow!
Case 2: Installed and commissioned functions that impacted integrity
This case covers a couple of examples where installed functions impacted integrity.
Project 1: Greenfield added to Brownfield
A new outlet facility was added to a site to transfer fluids to another location. This is a Greenfield (new
facility) that required shut down interfaces with Brownfield (existing facilities).
The new facilities have Emergency Shutdown (ESD) isolation valves to box in the inventory, a
depressurization blow down valve, high wattage pumps, and local manual ESD stations.
The Brownfield installation used dual trip circuits that each used an energized to trip solenoid valve for
tripping closed the ESD shutdown isolation valves, and the depressurization via blow down valves. This
requirement was due to relief systems inventory limits which meant the whole plant could not be
depressurized at same time, and staggered blow down required.