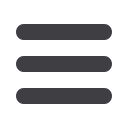

8
Disclaimer:
The content in this paper is loosely based on experiences, and have been embellished to bring out the salient points
against the objectives of this paper.
power source. The modification installed had been fully tested and operated as a stand-alone function
as it did not require the shutdown line as part of the function, and hence the fault introduced to the
shutdown system was not picked up.
The summary of this case study is that:
1.
No on-site changes to a design should be undertaken without a full review of the proposed
change.
2.
When decommissioned components are used a physical review of the as built/left state must be
ascertained before adding these components to a design.
This case shows that a well meant intention during the installation by using another decommissioned
module added a hazard into the safety system.
Case 3: Experience vs Competence
A small site did not have an Instrument Engineer. A change was being implemented on part of their
shutdown system with some new sensors and associated shutdown logic. This change had been
designed by a large engineering procurement contractor, who produced installation and site acceptance
testing documentation to be used.
The implementation of this change was through a local based company. The end user did not have an
instrument engineer but also had a project engineer. The end user project engineer was reliant on the
very experienced contractor supervisor, who overseen the installation and commissioning.
What could go wrong?
An independent functional safety assessment stage 3 post commissioning identified that the installation
and commissioned systems had gaps against the designed requirements. There were gaps in
management, documentation and on SIF capabilities. Typical findings were:
1.
The developed Site Acceptance Testing (SAT) and Commissioning procedures were not used by
the installation contractor.
2.
There was no evidence of full quality procedures used for installations and commissioning, and
thus no completion or commissioning dossier available.
3.
The test documentation available was sparse and did not provide evidence of testing of all
installed equipment. Such as; no installation quality assurance inspection certificates, some of
the continuity and earth test certificates for the instrument cable not dated, no continuity and
earth test certificates for the power cable, no installation inspection certificates, etc.
4.
There were no drawings (e.g. red lined or as-built available on site.
5.
There were calibration issues for the new radar level sensors, with different ranges and zero
datum points for same tank.
6.
The tank has a voted 1oo2 level sensors, but the level trip settings on each sensor was different.