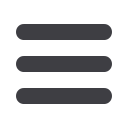

20
Mechanical Technology — February 2016
⎪
Materials handling and minerals processing
⎪
A
ccording to O’Bryan, Weir
Minerals’ global product man-
ager for screens and screen
media, achieving TCO goals
is possible by carefully and strategically
Using finite element
analysis assists in providing
lower cost solutions to customers.
In the coal processing industry, the total cost of ownership (TCO) model
is heavily dependent on strategies that lower the initial capital cost of
replacement screening machines. Coupled with this is an emphasis on
an improvement in the overall durability of traditional coal dewatering
screens towards lower operating costs. Weir Minerals’ Kurt O’Bryan (below
left) and Winchester Maphosa (below right) explain.
matching solutions to specific customer
needs and applications. He notes that
the company’s latest developments in
coal screening technology are focused on
increasing the size and mechanical dura-
bility of its coal duty vibrating screen line.
The Enduron
®
product range from Weir
Minerals – formerly known as Linatex
®
– concentrates on increasing throughput
and decreasing downtime.
The supply and installation of Linatex
screening equipment in the coal industry
spans a number of decades. The first
Linatex dewatering screens for a coal ap-
plication were supplied in 1983 to Anglo
American Coal’s Kleinkopje operation in
South Africa. Linatex dewatering screens
have since been successfully supplied
for fine coal applications, where they
significantly reduce the moisture content
of the fines product.
Over 450 Linatex banana and hori-
zontal screens in single and double deck
format, sieve bend static screens and
horizontal rotary screens have been sup-
plied to the coal industry for applications
ranging from primary dewatering and
desliming to dewatering of final product.
The customer list includes Anglo Coal,
BHP Billiton – now South 32 – Exxaro,
Coal dewatering solutions
for lower ownership costs