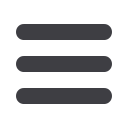

16
Mechanical Technology — February 2016
⎪
Proactive maintenance, lubrication and contamination management
⎪
Mario on maintenance:
P
reviously we discussed the prin-
ciples of proactive maintenance
and how it can be of benefit
to an organisation wishing to
improve the bottom line or enhance the
reputation and quality of service of public
entities. We examined the various strate-
gies and how it is important to use the
right combination for optimal results.
We spoke about the wide and rapidly
growing range of technologies that are
available to the reliability engineer and
how economics is making this more and
more attractive.
Whilst it is hoped that this was
informative, it completely omitted one
vitally important point that is the topic
for discussion here. Without it, many of
the benefits of proactive maintenance
will never be realised and sustainability
is practically impossible.
So what can this be?
If you have not already guessed,
it is of course the fact that everything
we discussed falls under the ambit of
physical asset management and that,
without an effective asset management
system in place, all manner of things not
only can, but will go wrong. In doing so,
one’s carefully thought out and imple-
mented proactive maintenance strategy
will be derailed. Strong words, and only
expressed with confidence because of the
myriad of personal experiences encoun-
tered. This is one instance where rather
than explain how things should be done,
the concept is better illustrated with
examples of what happens when things
have not been done as they should.
In one example that really stands out,
very large medium-voltage motors in a
production plant with four yearly sched-
uled outages were correctly identified
as critical by the reliability engineering
team. As a consequence, the motors have
been equipped with effective, but rela-
tively costly, continuous on-line condition
monitoring systems that have automatic
defect detection and predictive alarming
capabilities. Early warning will be given
so as to permit convenient intervention
to prevent unplanned failures, which
would far exceed the monitoring cost.
The monitors are installed, configured
and commissioned with appropriate
alarm set points.
All good so far – everyone is happy
that risk of unplanned failure is well
managed.
And indeed all is well for more than
Asset management and proactive
friends or foes?
In his column for this month, Mario Kuises talks about the importance of having an asset
management system in place to realise long-term benefits from proactive management
system investments.
Caption: Physical asset management is a structured approach in which techniques and processes are
determined and formalised to allow an organisation to both achieve and demonstrate that it is managing its
assets optimally.
two years. Then a failure occurs in one
of the motors, of exactly the nature that
should have been detected by the moni-
tor and prevented. All sorts of questions
are asked and, most importantly, why did
the investment in monitoring not pay off
as planned?
On investigation, it was found that the
monitors were standalone and under the
control of the reliability team. No one had
bothered to involve asset management/
maintenance or to connect the monitors
into a system to bring the predictive
alarms to the attention of anyone at all.
Nor were any measures put in place to
have the monitors inspected regularly to
check for alarm conditions. When the
monitor’s stored data was examined after
the failure, the records showed that the
monitor had detected the deteriorating
defect and had first been in low- then
high-level alarm for months, but no one
knew. More specifically, no one who was
in a position to recognise the importance
of the alarm and do something about it.
The above example relates to condi-
tion monitoring to improve plant reli-
ability. Let us look at another common
example where condition monitoring is
employed to improve plant efficiency.
Valves, glands, gaskets, steam traps,
pipes, pressure vessels and the like
deteriorate over time. If not attended to,
the consequence is huge losses – and
potential safety and quality issues – due
to compressed air, steam and gas leaks.
Many energy managers are well aware of
this and engage professionals to survey
their plant to locate, tag and report such
leaks so that they can be fixed and the
losses stemmed. This is recognised to
be one of the most basic and beneficial
energy saving interventions that any
plant employing these utilities can do.
It’s simple and obvious.
It is also obvious that no benefit will
accrue if the leaks are not fixed.
Why, then, is it not unusual to go
to the same site to conduct repeat leak
surveys only to find the same leaks previ-
ously reported still unfixed, with the tags
There is no point fixing the
symptoms. It is essential to get
at the root of the problem, which
occurs for one simple reason –
the physical asset management
system is deficient.