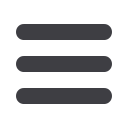

Mechanical Technology — February 2016
15
⎪
Proactive maintenance, lubrication and contamination management
⎪
occurred during thermal stress-relief of
the column during manufacture.
The possibility of an incorrect mate-
rial, such as ASTM A285 Grade A – with
similar properties to those found – having
been used in error was discounted fol-
lowing examination of the manufacturing
records. This, together with the uniformity
of loss of properties, tends to suggest that
the effect had occurred during stress-relief
heat treatment. Post-weld stress-relief
heat treatments, however, are usually
carried out at around 600 °C for short
periods, and do not generally degrade the
properties to any extent. This in turn sug-
gests that stress-relief heat treatment at a
higher than normal temperature is prob-
ably the cause, rather than exposure to
elevated temperatures during the fire. The
column would probably have collapsed
under its own weight had the reduction
of properties been caused by heating to
stress-relief temperature whilst erect.
The thickness measurements taken
on the column show a uniform loss of
wall thickness, but examination of the
vessel interior and internal structures do
not show any major corrosive attack. In
addition, the upper and lower vessels in
the column are of different materials to
compensate for different process condi-
tions, and a difference in the mean wall
thickness between the two would have
been expected had the material loss been
due to process corrosion.
This suggests that the loss of material
thickness is due to external corrosion due
to poor maintenance of the lagging vapour
barrier on the external surface.
Conclusions
That the column has suffered damage as
the result of exposure the fire is proven
beyond doubt. The wrinkle observed in
the shell close to the base is the result of
localised heating, which could only have
been the result of the fire.
The most serious damage to the col-
umn, however, is the deformation, which
presented as both longitudinal bowing
and localised ovalling, and the loss of
mechanical strength as indicated by the
reduction in hardness. The effects of the
fire cannot adequately explain either
of these phenomena, but both can be
explained by incorrect post-weld stress-
relief heat treatment during manufacture.
If it is accepted that both these fea-
tures originated during manufacture, it
may be argued that, despite their being
of a magnitude greater than that which
the design code regards as permissible,
the fact that the column has performed
satisfactorily for twenty years could be
taken as an indication that their presence
would not compromise the integrity of the
column, and on these grounds it could be
returned to service.
In the final analysis, however, the thick-
ness of the column shell was considered
too thin for extended service, and it would
have had to be replaced within a short
time, necessitating a second major pro-
duction interruption. A decision to replace
the column was therefore taken, based on
economic rather than technical grounds.
q
References
1 ASTM A516.
2 BS PD 2647.
3 Mechanical Properties of The BS En Steels: Woolman &
Mottram; Pergamon; 1964.
4 Author: unpublished work.
5 ASTM A370.
6 Boeing Aircraft Co. Specification: BAC 5617.
7 Auerkari P: On the correlation of hardness with tensile
and yield strength; Technical Research Centre of Finland;
Research Report 416; Espoo, Finland; 1986.
8 Author: unpublished work.