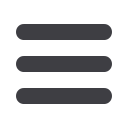

Mechanical Technology — February 2016
13
⎪
Proactive maintenance, lubrication and contamination management
⎪
was stainless steel to match the internal surface cladding of
the lower part of the column.
Two areas appeared to have suffered localised damage in
the incident, one close to the base and one just below the
mid-point, both taking the form of local bulging or wrinkling
of the shell. It was noted that both of these areas were on the
stainless steel clad portion, raising the fear of possible cracking
or disbondment of the cladding.
Dimensional examination
Once the column had been brought out of the plant and laid
horizontally, the bend in the longitudinal direction was clearly
visible (Figure 2). A di-
mensional survey showed
that the column was about
50 mm out of true at the
centre – with the bending
being fairly uniform along
the length – and presented
marked ovality in two dis-
tinct areas (Figure 3).
Shell thickness is an
important factor in the de-
sign calculations for any
pressure vessel, and thus a
detailed survey of the shell
thickness was undertaken
using a precision ultrasonic
technique. To ensure that accurate readings were obtained,
each area measured was cleaned by lightly grinding the surface
and removing the roughness due to corrosion, but removing
the minimum amount of material. Measurements were taken
over a series of regularly spaced positions located in a square
grid pattern covering the whole of the cylindrical portion of
the column. The results were a fairly uniform thickness with
a standard deviation of only 0.34 on a mean thickness of
7.71 mm (Figure 4).
No individual thickness measurement fell below the mini-
mum allowable thickness of 7.0 mm specified in the design.
Special attention was paid to the two wrinkled areas to deter-
mine if disbondment of the internal cladding had occurred, but
no sign of this was found.
Mechanical properties
Whilst mechanical properties were of paramount importance,
the need for non-destruction of the vessel necessitated an in-
direct determination technique. Quite clearly, the vessel could
not be moved into the laboratory and neither could material be
removed from it, and thus neither conventional tensile testing
nor high precision hardness testing using laboratory equipment
was possible.
A portable hardness testing technique had to be employed,
and the Equotip
®
system was utilised. This system uses the
velocity measurements from a spring-driven hammer as the
hammer approaches the surface to be tested and then again
as it rebounds. The difference represents the energy absorbed,
which can be related to Vickers hardness, HV
EQ
.
The results of a detailed hardness survey on the same posi-
tions as the thickness survey gave a mean value of 93.4 HV
EQ
,
with a standard deviation of 6.93 HV
EQ
, a remarkably uniform
result (Figure 5). It was noted that, despite their different ap-
Figure 3: Bending and ovalling results as revealed by dimensional survey.
Figure 2: Bending of the column
was clearly visible.
Figure 4: Measurements revealing fairly uniform, but low thickness in the shell.
pearance, having apparently been locally heated during the fire,
no significant reduction in the hardness of the two discoloured
zones was found.
Relating hardness to ultimate tensile strength in steels is
a well-known, though empirical, technique and can be ac-
complished with fairly good accuracy using conversion tables
published in a number of standards [5, 6]. Relating hardness
to yield strength, upon which the mechanical design of the
Figure 5: The hardness survey results showing uniformly low hardness.