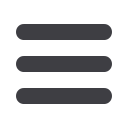

Mechanical Technology — February 2016
9
⎪
Special report
⎪
Above:
Based on its success at Kolomela, Efficient
Engineering now builds fully functional e-houses, includ-
ing the shells for the substations, motor control centres
(MCCs) and control and instrumentation (C&I) rooms as
single integrated modules, and fully equips them offsite.
Left:
A modular pump station was built by Efficient Power
to pump and additional 1 800 m
3
/h at a 40 m head from
the deepening pit.
Centre:
To accommodate pumps, decoupling vibration
dampers and reinforced mountings carry the 35 t of trust
down to the 3.0 t concrete mounting plinth below the
‘building’. Shuttering formwork and a steel reinforcement
cage was also incorporated below each pump.
Below:
Built into the housing structure is an overhead
crane to enable installation and servicing of the heavy
pumps and piping systems.
extra on the offsite modular construction
approach, R79-million was saved.
The main reason? “The provisional
and general budget virtually disappeared,
because all the work was done offsite.
Very few contactors had to be paid
for travel, accommodation or material
shipping costs to the site. In addition,
the contingency budget went unspent,
because there were no unexpected ad-
ditional costs due to onsite issues.
“And the knock on savings were outra-
geous. We closed a site with running costs
of R150-million per month five months
early. As a result, 1.4-million tons of ore
was put through the mine before it was
due to open – and the capital expenditure
for the development of Kolomela, which
was about R8.4‑billion, was paid off in
24 months,” Jackson reveals.
From electrical to mechanical
plant
Pit dewatering at Kolomela is achieved
via 16 boreholes that lower the surround-
ing water table. “The water is fed into
an eight-million litre water tank and it
is then pumped 18 km as potable water
to Beeshoek, into the Vaal Gamagara
municipal intake at up to 1 500 m
3
/h.
“While the mine had moved towards
offsite modular designs with respect to its
substations and MCCs, the pump house
itself experienced civil delays. We had a
fully functional MCC control room and
all of the medium-voltage infrastructure
onsite and operational, but the pump sta-
tion building hadn’t been completed. So,
while massively successful on the electri-
cal side, we were still being hampered by
delays on the civil and mechanical side,”
Jackson says, adding, “the budget for the
pump station building was originally in
the order of R1.8-million, but it ended up
costing well north of R4-million – and it
was more than eight months late.”
“Onsite construction of plant at re-
mote mines is such an onerous thing. A
project can be hampered by continuous
delays, due to late deliveries of inputs,
the wrong people being sent to site and
a host of safety and security restrictions
that make rapid progress impossible,”
he explains.
Following the success of Kolomela