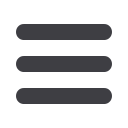

ENERGY + ENVIROFICIENCY:
FOCUS ON VALVES + ACTUATORS
at certain sections throughout the day since agitation operations
continue without interruption. The different pressure and flow re-
quirements for the various consumers presents an opportunity to
implement a control strategy that will allow compressed air to be
supplied more efficiently.
Pressure losses resulting from line friction
Air flowing over a long distance will be subject to relatively large pres-
sure losses as a result of line friction. To calculate this pressure loss a
few fundamental principles need to be taken into account. Owing to
the relatively large air flow speed, pipe wall roughness and long pipe
lengths, only turbulent flow conditions are assumed to be present.
The airflow in a pipe experiences resistance as a result of viscous
sheer forces. The wall roughness plays an important role in determin-
ing the friction factor,
ƒ
. Experimental methods are mostly used to
determine
ƒ
for a specific situation. The friction factor is a function of
the Reynolds number (
N
R
) and relative pipe roughness factor ( ) [2].
Figure 4
illustrates what is meant by the relative roughness of a pipe.
Figure 4: Relative roughness of a pipe [2].
When calculating the roughness of pipes that have been in use for
some time, the absolute roughness of new pipes can only be used
as estimates since the effects of rust and corrosion in the pipes will
result in larger relative roughness values of the pipes.
Using assumed relative roughness and Reynolds number val-
ues, the friction factor
ƒ
can be read off the Moody diagram shown
in
Figure 5
.
Figure 5: Moody diagram.
Air density is calculated using the standard equation of state for a
perfect gas [3]:
ρ =
Where the variables are:
o Density
-
ρ
[kg/m
3
]
o Temperature
-
T
[K]
o Absolute pressure
-
p
[N/m
2
]
o Gas constant
-
R
[N · m/kg
·
K]
For air, the gas constant is 287 N · m/kg · K at 298 · K, and 101 kPa [3].
The pressure loss,
∆
p = (p
1
- p
2
)
over a length of pipe can be calculated
using the following equation [4]:
∆
p = 4
ƒ
Where the variables are defined as:
o Loss of pressure
-
∆
p [Pa]
o Density
-
ρ
[kg/m
3
]
o Internal pipe diameter
-
d
[m]
o Pipe length
-
l
[m]
o Average velocity
-
v
[m/s]
o Friction factor
-
ƒ
[dimensionless]
From this formula it is clear that the
∆
p
over a length of pipe will
increase if:
• The pipe length increases
• The rate of air flowing through the pipe increases
• The air density increases
Air flow losses through air leaks
The compressed air lost through air leaks in a compressed air system
is a function of the pressure of the air in the pipe as well as the size of
the leak. Most of the formulas used to calculate the compressed air
lost through air leaks are derived empirically. The following formula
can be used to calculate the volumetric flow rate of free air through
a hole with a given size [5]:
V
f
=
Where the variables are defined as:
o Volumetric flow rate
- V
f
[m
3
/h]
o Number of air leaks
- NL
[dimensionless]
o Atmospheric air temperature - T
i
[
o
C]
o Line air temperature
- T
l
[
o
C]
o Line pressure
- P
l
[kPa]
ε
D
p
RT
l pv
2
d 2
ε
D
0.1
0.09
0.08
0.07
0.05
0.04
0.03
0.02
0.015
0.01
0.008
0.006
0.004
0.002
0.001
0.0008
0.0006
0.0004
0.0002
0.0001
0.00005
0.00001
0.06
0.05
0.04
0.03
0.02
Coefficientof friction f
ReynoldsnumberR
0.01
0.009
0.008
3 45 10
4
2 345 10
5
2 345 10
6
2 345 10
7
2 345 10
8
NL
× (T
i
+ 273)
×
P
1
/P
i
×
C
1
×
C
2
×
C
d
×
π
D
2
/4
C
3
×
T
1
+
273
37
February ‘16
Electricity+Control