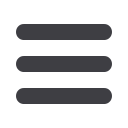

o Atmospheric pressure
- P
i
[kPa]
o Isentropic sonic volumetric flow constant - C
1
[7,3587m/s K
0,5
]
o Conversion constant
- C
2
[3600s/h]
o Isentropic coefficient of discharge for square edged orifice - C
d
[0,8]
o Leak diameter
- D
[mm]
o Conversion constant
- C
3
[10
6
mm
2
/m
2
]
It is clear from this formula that the air flow through the hole in the
pipe will decrease when the system line pressure, P
1
is decreased.
Pressure control methods
Automatic pressure control valves are used to control the air flowing
through a pipe. The valve opening can be adjusted so that pressure
loss over the valve will result in the required reduced system pressure
downstream of the valve.
Pressure transmitters installed in the air ring are used, not only to
provide pressure metering at the specific location where it is installed,
but also as a feedback process variable. This feedback process vari-
able is used in the PID control loop to adjust the valve opening so that
the pressure loss across the valve will provide the correct, reduced
downstream system pressure.
Case study
The surface air ring of the mine that was used in this case study con-
sisted of a pipe network that was approximately 40 km long.
Figure 6
is a simplified schematic layout of the mine’s surface
compressed air network.
Figure 6: Surface layout of case study.
The bottom three shafts shown in
Figure 6
are themine’smain produc-
tion shafts. These shafts require a supply pressure of 590 kPa during
peak production hours which start at 0700 and continue to 14:00.
ENERGY + ENVIROFICIENCY:
FOCUS ON VALVES + ACTUATORS
For the remainder of the day a pressure of 520 kPa will be sufficient
to sustain the system air pressure requirements of the end users in
this shaft. Most of the mine’s compressors are also installed at these
shafts. This allowed the compressed air supply pressure set point
to be regulated at the pressure required for the high pressure side
of the compressed air ring. For the implementation of the ring split
strategy, two control valves were required. The location of the valves
in the compressed air ring is indicated on
Figure 6
.
Figure 7
shows a typical pressure usage profile for a normal
production day of these shafts. This was also the pressure profile
of the entire compressed air ring that was used before the ring split
strategy was implemented.
Figure 7: Shaft pressure.
The two valves are controlled from the central control room and
isolate the high pressure side of the compressed air ring from the
low pressure side. A low pressure set point of 440 kPa is maintained
in the low pressure side.
It can be seen in
Figure 6
, that compressors are located on either
side of the compressed air ring. The compressors located on the
low pressure side are presently used as a backup in case additional
air is required on the low pressure side of the
ring. Because of the location of these
compressors and the fact that they
were used before the ring was split,
no accurate flow data was avail-
able to compare the difference
in flow rates before and after
implementation.
The effect of the reduced
pressure and air flow was ob-
tained by comparing the total
amount of compressed air used
over a period of one month with the
corresponding values when the power
baseline was originally measured. After imple-
mentation, the total amount of compressed air used was an average
of 191 728 tons per month.
Time in hours
High pressure side
650.00
600.00
550.00
500.00
450.00
400.00
350.00
300.00
250.00
1 2 3 4 5 6 7 8 9 10 11 12 13 14 15 16 17 18 19 20 21 22 23 24
Pressure in kPa
Shaft pressure
Electricity+Control
February ‘16
38