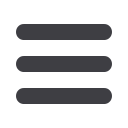

29
Chemical Technology • March 2015
In every supply chain there are activities that must be initi-
ated in anticipation of future demand. The specific activities
vary with the business, but generally include finished goods
production, semi-finished goods production or rawmaterials
purchasing. To maximise performance, these activities must
be planned with the best available information. Improve-
ments in forecasting and demand planning can reduce the
need to carry excess safety stock or have spare capacity sit
idle. In a fully integrated supply chain, production opera-
tions should be closely linked with demand management,
so a company’s operational plan can adapt as quickly as
demand changes.
Generating an accurate demand forecast is a critical first
step in the S&OP process, as it is the demand signal that
Spreadsheets are widely recognised as inadequate for
managing complex supply chains. They are typically
customised to fit the constraints of each plant and are
prone to errors and labour-intensive data gathering.
The interactive Planning Board in Aspen Plant Scheduler
provides an easy way to visualise and make changes to the
schedule as well as view inventory levels for multiple products
simultaneously.
Scheduling Case Study – NOVA Chemicals
NOVA Chemicals, a plastics and chemicals producer with
manufacturing sites strategically located throughout Canada
and the United States, wanted to standardise their supply
chain operations – processes and underlying technology –
for their polyethylene business. Due to fragmented business
processes, lack of automation and scheduling models that
were customised for each plant site, NOVA Chemicals was
forced to manage their supply chain in a largely manual
fashion, making it difficult to react to any type of business
change. The company lacked the ability to evaluate the
impact or to determine the best course of action for events,
such as price changes, shutdowns, raw material constraints
or weather-related factors. Furthermore, the lack of uniformity
between models broke down synergies between groups and
made change management very difficult.
By committing to a new, standard set of business
processes for all parts of the polyethylene business, NOVA
was able to migrate to six standard aspenONE Supply
Chain Management applications with a single design
throughout. The new business processes and technology
were automated and integrated, enabling NOVA Chemicals
to react quickly to changing business conditions, reduce
overall IT ownership and model maintenance and improve
data sharing and collaboration to increase their scheduling
horizon by 100%.
“Due to forward visibility, the scheduling horizon doubled,
increasing from 90 days to 180 days. This gave the
schedulers better raw material visibility and a better product
wheel.”
Zoran Stojecevski, Systems Analyst and Developer, NOVA
Chemicals
© 2014 Institution of Chemical Engineers (IChemE) and
Aspen Technology. All rights reserved. 11-4433-0314
S&OP Case Study – ¤15B specialty chemicals producer
in Europe
A €15 billion specialty chemicals producer based in Europe wanted to
ensure execution of reliable and cost efficient delivery of their products in
Central Europe. The company also needed to remove bottlenecks in the
production and distribution processes and to simultaneously optimise:
• Storage and transport capacities
• Logistics (mode of transportation, route, vehicle utilisation, etc.)
• Sourcing from shipping points
Additionally, the company needed to meet regulatory compliance
requirements to track CO
2
positions across ten European countries against
annual emissions limits.
This supply chain transformation was not an easy task considering the
complexity of their supply chain network, which includes more than 30 sites,
hundreds of resources, thousands of ship-to locations and a multitude of
raw material suppliers. The company did not have a global reporting system,
asset visibility or standard supply chain business processes across the
organisation. In fact, each country operated completely independent of one
another, tracking operations on desktop spreadsheets. To unify operations,
the company turned to Aspen Supply Chain Planner, a software application
that supports the S&OP process in the aspenONE Supply Chain Management
suite to achieve the following:
Optimise across 10 business units
Facilitate decision-making based on economics
Increase the transparency of their business processes
Perform both short-term (weekly/monthly) and strategic long-term (1-5
years) planning.
Through Aspen Supply Chain Planner, this specialty chemicals producer
easily determines alternative supply paths across the network and
dynamically selects optimal product source locations, based on physical
constraints and emissions limitations. By optimising their supply chain
to determine the lowest cost for each customer and by improving work
processes, data management and reporting visibility, this specialty chemicals
producer estimates that it will attain €20 million in annual benefits.
SUPPLY CHAIN
MANAGEMENT