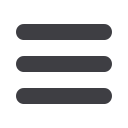

45
J
anuary
2008
www.read-tpt.comT
echnology
U
pdate
›
customer’s requirements in terms of ovality
and wall thinning. The custom machine
also features bi-directional communication
with the Eagle TMS-100 tube measuring
machine, to enable accurate parts to be
produced with the least amount of scrap
– essential for the small part runs required
for the project.
In addition to the custom EPT-100 XPH
hydraulic bender, Eagle also supplied an
EPT-25 EPS (25mm capacity) multi-stack
all electric CNC tube bender for use on
smaller pipe diameters. This machine was
also coupled with the Eagle TMS-100. The
multi-stack design of the bender minimises
tool changeover to optimise production
efficiency. All machines were delivered in a
time period of 12 weeks.
Eagle Precision Technologies Ltd
– Canada
Fax
: +1 519 756 0195
:
sales@eaglept.comWebsite
:
www.eaglept.comWorld’s ‘fastest’ arc
welding robots
Two new six-axis industrial robots for arc
welding, claimed to be the fastest on the
market, have been introduced by Motoman
Robotics, UK.
The latest all-electric models, Super
Speed SSA2000 and SSF2000, are 40
per cent faster than previous robots owing
to advanced motion control of the axis
movements. The resulting 15 per cent
reduction in weld cycle times significantly
raises productivity, and weld cycles are
speeded further by minimising arc on/off
time.
The SSA2000, with a 3kg payload, has
the same upper arm as the Motoman
EA1400N Expert Arc robot. Welding cables
are integrated and the torch is mounted in-
line with the welding axis, which eliminates
cable interference, reduces cable wear and
simplifies programming. The SSA2000 is
suitable for multiple-unit installations where
two or more robots interact closely, and
for applications involving areas that are
difficult to reach or where there is a risk of
interference from fixtures.
The SSF2000 robot, with a 6kg payload,
is similar to Motoman’s HP6 model and is
designed for arc welding with traditional
external cabling and handling. It can be
used with vision sensors and with torches
that have an integrated wire feed.
Both of the new welding robots, which have
a reach of nearly 1.4m and a repeatability
of ±0.08mm, are controlled by Motoman’s
NX100 controller, featuring robust PC
architecture, Windows CE programming
pendant, and easy-to-use Inform III
programming language.
Motoman Robotics (UK) Ltd
– UK
Fax
: +44 1295 267127
:
information@motoman.co.ukWebsite
:
www.motoman.co.ukEssential CNC machining units
for automatic manufacturing
Arla Maschinentechnik GmbH, Germany,
manufactures CNC controlled machining
units, which are modular components
consisting of spindle and slide units.
All units are directly driven by servomotors,
providing high stiffness in radial and axial
direction. The machining units are designed
for high torques in order to realise a solid
automated manufacturing process with a
very low cycle time.
The revised DUM models with integrated
motor spindle provide very high torques and
are also available with internal tool cooling,
and an optional manual or automatic tool
clamp. The concentricity of the spindle units
is less than 0.002mm, and according to the
model size, the supported tools must meet
the HSK standard (HSK 50-125).
The company can also supply solutions for
two or three axes. Typical applications are
in the automotive and aircraft industries.
Arla Maschinentechnik GmbH
– Germany
Fax
: +49 2267 658570
:
info@arla.deWebsite
:
www.arla.deHigh-speed bevelling, facing and counterboring
Protem GmbH, Germany, produces the US-HSB series, designed to bevel, face and
counterbore tube and pipe at extremely high speed.
Fully hydraulic, starting with the inside clamping system, the tool holder rotation and the
feeding of the tools, the machines can be used either in the workshop as prefabrication
PFM, or on-site as bevelling tools for high quality orbital welding. The machines will
perform any high quality welding geometry preparations, from standard steel pipes to
stainless steel, duplex, super duplex and others commonly used in the modern field of
welding.
The machines feature a lifting bracket to enable easier transportation and positioning
inside the tubes to be bevelled, and an inner self-centring hydraulic clamping device
requiring only one operator to handle the machine.
Two inside profile tracking tool holders rotate simultaneously on the tool holder plate to
perform the bevelling, facing and/or counterboring. If necessary, all preparations can
be done at the same time and at a very high speed, on any oval pipe, leaving a root
face at a constant width, optimally for the high standard bevel geometry in modern
orbital welding.
Protem GmbH
– Germany
Fax
: +49 7247 94 68 62
:
info@protem-gmbh.de•
Website
:
www.protem-gmbh.de›
Arla machining unit with motor spindle
fi
Motoman’s two new Super Speed arc welding
robots, SSA2000 (left) and SSF2000