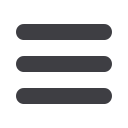

J
anuary
2008
www.read-tpt.com48
T
echnology
U
pdate
›
Laser cutting in sports car
chassis production
Caterham Cars, UK, celebrated the 50
th
anniversary of its iconic sports car with a
two-day event at the Donington Park racing
circuit. Created by the late Colin Chapman
and launched as the Lotus Seven, the
car was re-named the Caterham Seven
in 1973 when the former Lotus dealership
headed by Graham Nearn purchased
the manufacturing rights and re-started
production.
The Seven’s design is based around
Chapman’s ethos of ‘adding lightness’, and
while Caterham has refined and enhanced
the original design, the car remains much
the same in terms of appearance and
construction. However, while the traditional
tubular chassis is instantly recognisable,
the method of manufacture has undergone
substantial changes.
One of the most significant productivity
improvements in recent years has resulted
from a switch to tube laser machining of the
numerous individual components needed for
the variations of the ten or more Caterham
Seven chassis produced every week by
subsidiary company Steel Fabrications
Ltd, UK. This investment in new production
techniques has also contributed to a 12 per
cent greater torsional stiffness, that has
further improved the car’s road-holding
capability.
Steel Fabrications uses a BLM Adige LT120
LaserTube with a capacity from 12mm to
120mm OD tube or box section, to cut and
profile steel chassis components prior to
welding. Supplied by BLM Group UK Ltd,
the LT120 takes up to four tons of 6.5m
tube in its bundle loader, and nests finished
parts cut to an accuracy of 0.1mm at the
other end. As well as cutting and notching
tubes for chassis, wishbones and A-frames,
the LaserTube’s diffusion cooled CO
2
laser
source pre-cuts rivet holes in the chassis
components, reducing the time taken to
attach body panels.
Chassis components are stored in racks
ready for making up a ‘kit of parts’, a key
element in a production process that has
to deliver each chassis complete with
body panels to the assembly facility on
schedule, within budget and to the agreed
specification.
The latest parametric software is used
to design the chassis and to model its
component parts, and this CAD data
provides the basis for programming the
Siemens Sinumerik 840D CNC of the LT120
tube laser cutting system.
Joints between tubes that would have been
impossible or too expensive to produce by
traditional machining methods take just
a few minutes programming for the tube
laser, with prototypes and re-designs also
requiring just a few minutes to program.
The accuracy and repeatability of laser cut
parts ensure they always fit the welding jigs
without further dressing.
Chassis components are designed for
ease of fabrication, with tabs and profiles
combining to minimise the time needed to
assemble them in a welding jig prior to robot
welding. Once the chassis is complete it is
washed in a series of phosphate baths to
remove all traces of dirt and grease, before
being powder coated and the body panels
attached.
BLM Group UK Ltd
– UK
Fax
: +44 1525 402 312
:
sales@blmgroup.uk.comWebsite
:
www.blmgroup.uk.comBLM SpA
– Italy
Fax
: +39 031 715911
:
export@blm.itWebsite
:
www.blmgroup.comfi
The Caterham Seven’s welded chassis is phosphate washed and powder coated prior to fitting of the body
panels
fi
The BLM Adige LT120 tube laser is capable of
cutting tube components to an accuracy of 0.1mm
›
The Caterham’s low mass makes it inherently agile