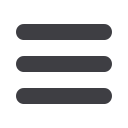

J
anuary
2008
www.read-tpt.com46
T
echnology
U
pdate
›
Installation of an all-electric tube bending
machine has helped White Brothers, the
official developer and supplier of 4-stroke
exhausts to Factory Yamaha, to bring its
bending process in-house and slash the
time it takes to prototype new designs.
The Unison Breeze machine has allowed
the company to replace a sub-contracted
prototyping fabrication process that used
to take up to two weeks, with turnaround
times now measured in hours. The much
greater control over the bending process
enabled by the company is also helping the
development team to experiment more, and
produce optimum shapes for its customers
more rapidly.
White Brothers is renowned as an innovator
in high performance exhaust systems for
motocross motorcycles and all-terrain
vehicles. Its range includes replacement
silencers, and complete exhaust systems
with shaped head pipes.
Expert attention to the shape, diameters and
angles used in the flow path ensure that the
company’s unique exhausts deliver more
power for riders. The products also reduce
weight substantially – one exhaust employs
titanium tubing and a carbon fibre shell for
example, for an ultimate combination of
strength and weight reduction.
The equipment installed at White Brothers
is a 3" (76mm) multi-stack all-electric
tube bender from Unison’s Breeze range.
The machine is used for both
development purposes, and for a
majority of the regular production.
Conventionally, a multi-stack tooling
arrangement is used to allow complex
shapes to be produced without tool
changes. White Brothers exploits
this feature to additionally speed up
production, by fitting combinations
of bending dies that allow the most
common types of head pipe to be
fabricated without reconfiguration.
In combination with the software-controlled
configuration process of the all-electric
machine, this allows batch changeovers
in minutes. In this way, the company often
manages to fabricate batches of as many
as 10 different product lines before stopping
the machine to swap tooling.
When bringing the tube bending process
in-house, White Brothers opted for an all-
electric architecture. Whereas most tube
benders today are powered hydraulically,
and need to be carefully set up for each
bending task by a skilled fitter, Unison’s
machine employs electric servomotors to
control the bending process. This provides
very precise bending under software
control, allowing each operation to be
configured automatically from downloaded
design data.
The technology is well suited to White
Brothers’ batch production environment
where exhaust pipes are often fabricated
in relatively small quantities of fifty or so.
The inherent accuracy and repeatability
offered by the Unison machine, which relies
on closed-loop axis control techniques and
is immunity to variations in temperature,
means that the first part made is usually
correct, and the rest of the batch can be run
immediately.
Unison
– UK
Fax
: +44 1723 582379
:
enquiries@unisonltd.comWebsite
:
www.unisonltd.comHorn Machine Tools
(US agent) – USA
Fax
: +1 559 431 4431
:
hmt@sierratel.comWebsite
:
www.hornmachinetools.comGlobal supply of
seamless steel tube
Ningbo New-Era Steel Tube Co Ltd, China,
handles both the import and export of
seamless tube. The company, which was
established in 1987 to manufacture and
distribute seamless steel tube, has four
wholly owned manufacturing enterprises.
The company produces cold drawn tubes
in the range 5-76mm x 0.5-10mm, and cold
rolled precision tubes in the range 10-90mm
x 0.5-18mm, to various American, European
and Japanese standards.
The company’s total production volume is
more than 1 million tons and 60 sets of cold
pilger mill per year. The company uses a
wide range of steel grades, and its products
have been exported around the world.
Ningbo New-Era Steel Tube Co Ltd
– China
Fax
: +86 574 87715158
:
wangyibo.jennifer@gmail.comWebsite
:
www.xjygg.com.cnSteel and brass tube equipment specialist
Wenzhou Yongdeli Machinery Co Ltd, China, specialises in producing steel tube and
brass tube equipment. The company has established an enterprise research institute
consisting of more than 20 professional experts in different areas of technology.
The company’s double-line cold rolling
mill has gained more than a dozen
patents, and was listed in the 2001
National-level Torch Program project.
Wenzhou Yongdeli’s products are
designed to provide precision, efficiency,
economy and technology, and the
company has passed ISO 9001:2000
quality
system
certification.
The
company’s production includes single and double line cold rolling mills, straightening
machines, three-roller rolling machines, and various metallurgical processing
equipment. The company exports mainly to Europe and America.
Wenzhou Yongdeli Co Ltd
– China
Fax
: +86 577 86922566 •
:
jixie0577@163.com•
Website
:
www.yongdeli.net›
Wenzhou Yongdeli’s LG250 cold rolling mill
Electric bending machine speeds manufacture
of motocross exhausts
›
An all-electric tube bender from Unison has helped White
Bros to bring bending process in-house and slash the time
it takes to prototype new 4-stroke exhaust designs