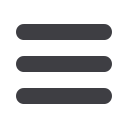

98
Wire & Cable ASIA – September/October 2015
www.read-wca.comFigure 6
, caught by a CCD matrix at the place of the wire,
shows the size of the (white) light line perpendicular to the
wire axis.
The Gaussian shape of the energy density in the light line
makes the efficient width at about 20μm.
Then the spot size along the wire axis (Line Resolution:
LR) is about constant, but on the circumference
(Circumference Resolution: CR), it fluctuates proportionally
to the wire diameter (r*α).
The line resolution on the wire depends only of the light
source system, not of the sensor.
To succeed in this development, one key point was
the light sources. They must be small and fast, but
generate very homogeneous light beams with uniform
characteristics. They have been specially and successfully
developed for this application.
Another key point was the sensor technologies. For the
smallest range, it was necessary to use a highly sensitive
sensor but one that was also very fast.
The movement of the wire with the rotation of the light
source generates an elliptic scan of the surface and a
continuous image on the sensor.
Image computing
The sensor must be able to characterise the size and the
shape of the defect according to the requirements of the
user.
The SQM computes in real time the perimeter (P) and the
surface (S) of the defect.
The ratio R = k*S/P
2
gives information on the shape of the
defect. k = 4π. In this case, R = 1 for a circular defect. It
tends toward zero when the defect elongates. Then R and
S are two key detection parameters.
In order to have homogeneous resolution, the line speed
is measured by the SQM (pulse counting) and the diameter
is a user parameter. Then the scanning frequency is
adjusted automatically.
Test results
At the time of writing, the authors were just at the start of
application and conducting industrial tests.
Still in laboratory conditions, a stainless steel wire 0.38mm
in diameter (15mils) was moved and this generated marks
or scratches.
In both cases the blue line determines the periphery of the
defect. Unfortunately the display is cut right on the top of
the wire where the marks are.
Nevertheless, it shows the computing analysis that works
all around the wire. The surface quality of the wire can also
be seen. Image calibration must be made on a smooth
surface of the wires.
This is also a process to develop to be able to deliver the
reference wires.
❍
❍
Figure 6
❍
❍
Figure 5
:
Front view of the system
Source/Photo-sensor locations
Zone 1/sensors A+C
Zone 2/sensors B+A
Zone 3/sensors C+B
Photo-sensor A
Ring of elementary light
sources
Measurement area
Photo-sensor C
Photo-sensor B
Zone 1
Zone 2
Zone 3
❍
❍
Figure 7
:
First case, one large side inked mark. Reading at
25kHz