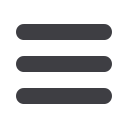

wire Southeast Asia 2015
95
wire Southeast Asia – BITEC, Bangkok 16
th
-18
th
September 2015
• Wide specialised range for the most
varied applications, eg buttwelding
machines for steelcord; battery-
operated parting guns for steelcord
or steel strands; electric wire
buttwelding guns; high-output butt-
welding machines for production of
wire-made mass articles; and
special-purpose welding machines,
tailored to individual customer needs
August Strecker GmbH & Co KG –
Germany
Website
:
www.strecker-limburg.deTroester GmbH
Stand: J19
Troester GmbH & Co KG is a supplier of
machines and complete lines for the
cable manufacturing and rubber
processing industry, comprising CV lines
for XLPE and rubber cables, silane lines,
sheathing and insulation lines.
The company will be presenting its latest
technology on:
• High voltage CCV and VCV line
concepts for XLPE power cables up
to 500kV
• Medium voltage CCV lines (35kV)
• Sheathing lines for medium and high
voltage cables
X-Compound, the new company of the
Troester Group, will also join the booth to
present its kneader technology for the
continuous compounding of HFFR, PVC,
XLPE, semi-conductive materials and
EPR/EPDM.
Troester GmbH & Co KG – Germany
Website
:
www.troester.deUpcast OY
Stand: L17
Utilising recycled copper in the process
of casting OF-Cu rod has long been the
target for manufacturers. The reason is
simple and obvious: cost efficiency.
Upcast OY has developed its continuous
casting technology and machinery to
meet the requirements for using 100 per
cent recycled material, or scrap as many
operators call it, in the OF-Cu rod
process.
Using recycled material in the Cu rod
casting process has been very
challenging with regard to both the
quality control and the mechanical
processing of the material.
The casting process itself does not
remove the possible metallurgical
impurities of the raw material. Therefore,
it was recommended to charge only
small quantities of recycled material
together with the pure copper cathodes.
This required extra manual work from
operators, increasing the workforce.
With consistent development work and
understanding the importance for the
customers Upcast has been able to
change the situation.
The first Upcast OF-Cu rod continuous
casting line utilising 100 per cent
recycled material from the other internal
processes was delivered a year ago and
has since been successful in operation.
The automatic charging technology of
the new line is designed specifically for
recycled material. The final product
determines the criteria and limit values
for the raw material. Thus, the purity of
the recycled material is crucial for the
process.
Using scrap from other processes of the
same manufacturer assures that the
material is exactly the kind needed for
the casting process.
In the past the charcoal covering the
melt in the furnace has caused some
problems in the material feeding and
melting process of recycled material by
preventing smaller pieces from fully
sinking into the melt.
This can be prevented by pre-handling of
the material, and the new line is also
equipped with a hydraulic press forcing
all the pieces into the melt. The
automated processes together with the
new advanced control system have also
added to production efficiency.
For example, the automatic transfer of
the melt results in less manual work, and
the probability of human error is
minimised.
The remote access system allows for a
very quick fault detection followed by
fast repair actions. This is extremely
important in order to avoid longer
disturbances or breaks in the process.
Furthermore, the system allows the
customer to have all the possible
process data enabling them to make
adjustments for efficiency optimisation.
Upcast OY – Finland
Website
:
www.upcast.comUyar Celik Endustrisi
San Tic
Stand: C01
With more than 50 years’ experience
Uyar Celik was founded with the aim of
fulfilling the need of qualified industrial
steel in the global market.
Sales are made directly from stock from
its head office and warehouse in Ikitelli,
Istanbul, Turkey, while plants in Europe
and Asia, and branches located in
Hadımkoy, Istanbul, and Dilovasi, Izmit,
are active on hot rolling and cold
drawing processes as well as selling
directly from production and stock.
The company also imports various types
of long steel products which are not
produced in Turkey or are produced
under limited conditions.
The manufacturing is carried out to EN
and ASTM standards, depending on the
domestic and international customer
demands.
Uyar Celik Endustrisi San Tic AS –
Turkey
Website
:
www.uyarcelik.com❍
Covering a variety of needs in the wire
and cable industry
❍
The triple extrusion group from Troester
❍
The Uyar Celik plant and headquarters