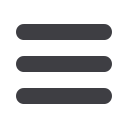

97
www.read-wca.comWire & Cable ASIA – September/October 2015
The energy gleamed to the observer (sensor) is strongly
modulated by the surface quality; roughness, colour
(absorption) and flaw, but also the local shape of the cylinder.
Then, rotating the light around the wire axis will also rotate the
gleam on the surface referring to a fixed observer.
This generates a circumference image. When the wire
moves, it develops a complete surface image of the wire.
If the design is well made, any small surface defect,
colour or shape change will produce locally a significant
reduction of the gleamed energy to the sensor.
Figure 2
shows the key parameters of the principle:
On the section plan of the wire, the incident light rays are
almost parallels. Perpendicularly to the wire axis, each
source beam is focused in a narrow line.
2*α, comes from the angular aperture of the optical
system. It determines the spot size on the circumference of
the wire: r*α.
2*β, comes from the angular incidence of the light source.
If “A” is the surface absorption/diffusion factor of the wire,
the light energy “E” received by the sensor is:
E = A*ie* r*α*cosβ
The consequences of these relations are:
• Spot size (r*α) proportional to the wire diameter, which
is quite satisfactory, and of the angular aperture of the
optical system
• The energy received by the sensor fluctuates with the
angular incidence of the light source by cosβ. Using
three sensors, “β” fluctuates within ±60° per sensor,
generating a signal amplitude modulation by 50 per
cent. This is compensated by a correction factor in
order to display a flat response. With five sensors, the
direct fluctuation falls to 20 per cent
• The energy received by the sensor is also directly
proportional to the wire diameter. This means that
the incident light source energy “ei” must be adapted
accordingly, but also the sensor technology depending
of the range of diameters to check. The smallest
diameter able to have been checked properly was from
a tungsten wire (black colour) of 10μm
• The A factor has a significant impact either by diffusing
the energy (roughness) or absorbing the light ray at
850nm
Another important effect is the shape change along the
wire axis (lump, neck, flaw) that deflects the reflected rays
out of the angular aperture of the sensor.
Design
To rotate the lighting point a ring of light sources was
made around the wire axis, with only one source light on at
once.
Switching the lighting from source to source generates a
rotating light point around the wire. Three sensors at 120°
simultaneously check the gleamed energy on the surface
of the wire.
The light source system concentrates on each source
beam in a narrow line perpendicular to the wire axis. The
beam is about parallel to the other plan.
The thickness of the line determines the resolution
on the wire axis. Then the sizes of the sources must
be small and the optical system good enough for the
application.
Polished
Diffusing
❍
❍
Figure 3
:
Roughness effect
❍
❍
Figure 4
:
Shape changing effect. Modelling image
❍
❍
Figure 2
:
Lighting
E = A*ie* r*α*cosβ
Sensor optical system
Wire, radius
7
r
8
Light source rays,
incident energy
7
ie
8
❍
❍
Figure 1