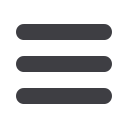

56
Wire & Cable ASIA – September/October 2015
www.read-wca.comTechnology
news
MANUFACTURERS
of
cables,
specifically automotive and data
cables, require a reliable conductor
preheating, to ensure an optimum
adhesion of the insulation on the wire,
and a controlled foaming.
With the Preheater 6000 TC
(temperature controlled) Sikora has an
advanced
solution
for
precise
conductor preheating, the basis for
high-quality cable production and
repeatable control of the production.
In only a few applications, it may be
sufficient to control the output power
of a conductor preheating device only
depending on the conductor size and
type, the line speed and the required
temperature.
However,
there
are
numerous
influences on the accuracy of the
conductor temperature, such as the
ambient temperature, the initial
temperature of the conductor and
particularly the development of the
temperature of the wire guiding
short-circuit wheel within the first ten
to 20 minutes after starting the
production or after an interruption of
the production.
The Preheater 6000 TC is positioned
before the extruder and inductively
heats the conductor to the desired
nominal value. The integrated IR
camera ensures a non-contact
measurement of the wire temperature
at the output of the preheating device.
The controlling module of the
Preheater 6000 TC continuously
adjusts the power of the preheating
with the result that the wire always has
the nominal temperature, inde-
pendently of conductor material, the
dimensions of the conductor and the
line speed. No further setting is
necessary.
LED displays directly on the Preheater
6000 TC show the measured
temperature at different perspectives.
The integrated, non-contact temp-
erature control makes the Preheater
6000 TC unique. It is available for
temperatures up to 250°C, for a
product diameter of 0.32 to 4.5mm
(0.08 to 16mm²) and for a line speed of
up to 2,500m/min.
Three device models are available for
the power range of 10, 20 and 30 kW.
A power calculator at
www.sikora.net/powercalc helps choose the optimal
device.
The Sikora temperature measuring
system is also available as the
stand-alone system Wire-Temp 6000.
Sikora AG – Germany
Website
:
www.sikora.netConductor preheater with integrated temperature
measurement and control
❍
Conductor preheater with integrated
temperature measurement and control
At a time when machine-to-machine
communication is proliferating in the
industry, Technifor has risen to the
challenge with a new range of laser
marking machines that are making their
mark as a true model of integration –
Laser Solution F-Series.
The
new
electronics
offer
communication tools natively, allowing
continuous and instantaneous inter-
action with the various workstations
integrated into the chain of production.
Dedicated and generic inputs/outputs,
TCP/IP Ethernet, Profinet, RS232, USB,
the configuration, control and data
recording options are cutting-edge and
allow for remote control.
The new connections eliminate the
need for costly adapters and offer the
prospect of a single central server
managing a factory’s entire fleet of
lasers.
Ultra-fast, the choice of high-
performance electronic components
has resulted in marking equipment that
is 50 per cent more time-efficient than
the previous generation.
Available in a range of powers from 10
to 50W, the Laser Solution F-Series
permits the direct and permanent
marking of a wide variety of parts and
materials (plastics, metals, ceramics,
etc).
From surface marking to deep
engraving, it executes 1D and 2D
codes, guaranteeing faultless scanning.
These new laser machines offer a real
technical advantage to integrators and
manufacturers who need to install
marking stations on production lines.
Highly compact, the marking head is
adapted to industrial constraints: small
spaces, extreme conditions of
temperature and vibration, it is robust
and protected from dust or other
splashes (class IP54). The solution can
be integrated with no necessity for
filtration or additional enclosure and it
is immune to electromagnetic inter-
ference.
Designed to minimise installation costs
and time, the equipment is easily
interfaced with a PLC thanks to
pre-programmed controls.
A control screen with integrated HMI
displays the operations in progress and
offers
self-diagnostic
capabilities:
machine status, event history, backup
files and maintenance messages are
accessible in real time.
Benefiting from a wealth of application
experience with major car and
automotive parts manufacturers, in
precision mechanics, aeronautics,
medical and other leading-edge
sectors, Technifor delivers end-to-end
equipment meeting its customers’
expectations.
Technifor – France
Website
:
www.gravotech.comMarking innovation and performance