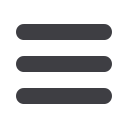

1/2016
|
31
I
n September 2012, some 40
UPM leaders convened for a
target-setting meeting in the
lead-up to the PM3 (paper
mill) project at the Changshumill in
China. They decided to name it ‘the
Panda project’, as the panda has an
important place in Chinese culture
and history, symbolising harmony
with nature.
Sustainability and safety have
indeed been cornerstones in this huge
EUR 277 million project, which was
completed in December 2015. The
new paper machine can produce up
to 360,000 tonnes of high-quality
labelling materials and wood-free
uncoated papers annually. This
‘swing-concept’ machine also makes it
possible for the mill to shift between
grades.
“It’s been a very challenging project
since it’s different from anything we
have done before. We have to be able
to produce two completely different
products, and we couldn’t just copy
and paste our familiar templates.
Instead, we had to innovate something
wholly new,” says PM3 Project
Director
Timo Heinonen
, who has
previously been involved inmany new
paper machine and rebuild projects in
different roles.
early stages and was distributed to
every new supplier. An OHS team
was set up consisting of five full-
time supervisors, one nurse and one
assistant.
In order to improve safety levels
and enhance safety awareness,
the OHS team built a Safety
Induction Training Room that could
accommodate 60 people at a time.
“All personnel involved in the PM3
project – from senior management
to construction units and workers
– had to undergo safety training
before being approved entry into
the construction area,” says
Tony
Liu
, Occupational Health and Safety
Manager of the Panda project.
Every week, the OHS team also
carried out several unexpected “safety
walks”, inspecting the entire project
site for full compliance with safety
protocols. Violations were punished
with fines.
Old and new partners
Heinonen andmost other people in
the project teamhave many years of
experience, andmany were already
involved in the Changshumill’s PM1
project between 2003 and 2007. One
of them is PM3 Project Manager
Steve Masterson
, who continued
“I’m very confident that we’ve
found the solutions to reach the
quality targets set for the products
we’re going to produce,” he adds.
Emphasis on safety
Safety has been a top priority
throughout the entire project.
Heinonen says he is very happy to
have reached over four million hours’
work time without a single lost time
accident (LTA).
LTA is a leading safety
management indicator referring to
an accident occurring at work and
resulting in at least one full day of
absence fromwork duties. At UPM,
the company-wide target was already
very challenging: 5. The target for the
PM3 project was even lower: 0.8.
“From the start, the most
important priority was ensuring
that nobody was injured, and we’ve
worked hard to achieve this target. We
implemented strict safety rules and
we have spent more time on this than
in any other project I’ve worked on
previously,” says Heinonen.
Since dozens of contractors and
suppliers were to be involved in
the PM3 project, a comprehensive
occupational health and safety (OHS)
plan was produced in the project’s
>>