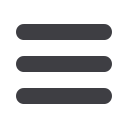

1/2016
|
35
When UPMfirst arrived in China in
the late 1990s, it took over an existing
plant at a site in Changshu in Jiangsu
province, not far from Shanghai and
with an excellent port on the Yangtze
River, the most important river in the
history, culture and economy of China.
UPM then inherited PM2, one of the
existing paper machines at the mill.
In 2004, when UPM invested in a
new paper machine, they named it PM1.
This huge investment increased the
mill’s fine paper capacity by 450,000
tonnes per year, bringing it to 800,000
tonnes when PM1 was inaugurated in
2005.
PM3 will now increase the mill’s
capacity to well over one million tonnes
per year. It will also enable the mill to
offer multiple grades of paper.
“This has been a fantastic project so
far. Everything has gone so smoothly,”
says
Pentti Putkinen
, General
Manager of the UPMChangshumill.
“Even though PM2 is a kind of
swing machine that can produce both
coated and uncoated paper, we haven’t
had a machine that can alternate
between uncoated paper and labelling
materials,” he says.
“In fine paper you typically want to
maximise bulk, but label paper is very
dense and has no filler at all, so these
two paper grades are total opposites in
this respect,” says Putkinen.
One of the world’s
best paper mills
The UPM Changshu mill is state-of-the-art in many key respects:
it sets the global benchmark for efficiency, technology, safety
and environmental performance.
“Our challenge now is to minimise
grade change losses so that we lose as
little time andmaterials as possible in
the shifts. I’m very confident that we
can do it,” says Putkinen.
The Changshumill has a reputation
for being one of the best mills in China.
It has achieved excellent results in
terms of resource efficiency. It has cut
water consumption by 65 per cent,
energy consumption by 25 per cent and
waste to landfill by 60 per cent over the
past ten years, and 99 per cent of the
mill’s waste is now recyclable.
“I think that our mill is one of the
best in the whole world when it comes
to efficiency, technology, safety and
environmental performance,” says
Putkinen.
COMPREHENSIVE
TRAINING
UPM’s Tervasaari mill in Finland is
a world leader in labelling mate-
rials, or release liner. The mill has
recently served as a ‘mentor’ to the
Changshu mill, teaching new skills
to the Changshu mill staff, who have
had to learn to use a new technology
that is totally different from that used
for making fine paper.
UPM China provided plenty of
training to operators of the new
paper machine. Two groups of
around 15 people went to Finland for
two-week training sessions and also
received training at a customer’s site.
“They learned a lot during the day
and enjoyed socialising in the
evenings. We even heard that some
of the guys went fishing and caught
some perch, which they cooked
for dinner,” says
Tuija Rinne
, Vice
President for Human Resources at
UPM Paper Asia.
UPM Paper Asia employs some
1,550 people. According to Rinne,
when PM3 is operational, the
Changshu mill will have around
1,000 employees.
“I think that our mill is one
of the best in the whole world.”
Pentti Putkinen, General Manager,
UPM China
Pentti Putkinen