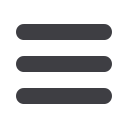

32
|
BIOFORE
working at the mill for some time after
the installation of PM1.
“Inmany ways, these two projects
have been similar but there are also
differences,” says Masterson. “For
example, this time much of our
equipment has been sourced from
China, while before almost everything
was imported. However, the biggest
difference – and challenge – has been
the swing-concept machine. Both the
machinery and the process itself have to
be flexible so that we canmake quick and
effective grade changes. For example,
the machinery has to be completely
cleaned and reset for the next product.
“This has not only been a big
challenge for the project team; it will
also be a big challenge for the mill’s
operators as they take over,” says
Masterson.
Finnish consultancy Pöyry and
Chinese design institute Haisumwere
chosen as the engineering companies.
Voith of Germany was selected as the
supplier for the new paper machine.
This marks the first time that UPM
bought a machine of this size fromVoith.
“We were very happy to be selected
for this UPM contract. This has been
a big and demanding project, because
the machine will be producing different
kinds of paper grades,” says
Johannes
Rimpf
, Voith’s Project Manager for the
PM3 project.
On-site installation of the machine
started inMay 2015, after which Voith
worked closely with UPM’s project
teamuntil early December, when
the machine was handed over to the
Changshumill.
“It has been a high quality project
all over, especially in terms of safety,”
says
Wolfgang Windisch
, Installation
Manager at Voith. “The regulations are
strict and the safety targets are always
followed up. I believe that UPM’s
‘Finnish touch’ has contributed to the
project’s success on the safety front.”
Tight schedule
Even though the schedule was tight,
UPM’s project teamplanned the project
so thoroughly that there were no severe
delays.
The project commenced with the
construction of roads, buildings and
other engineering.
Nantong Construction Group
(NTCC) of China was selected as the
general construction contractor.
Nantong and UPM go way back, as
Nantong was also involved in the
construction of the PM1 project from
2003 to2005. All of the subcontractors
were selected by UPMand are mainly
local companies.
“We managed to stick to the
schedule despite the fact that we had
many more rainy days than expected.
During 2014 we lost 38 days due to
rain, forcing us to stop all construction
work for safety reasons and due to
difficult working conditions,” says
Antti Mankki
, Project Construction
Manager.
“This was the first time
we’ve completed a project in
China involving so many local
suppliers and engineers.
It has been a very positive
experience for me.”
Timo Heinonen,
PM3 Project Director
People concentrated in the control room.
Timo Heinonen