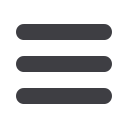

48
|
BIOFORE
soon be fed into the chipper? “Yes
indeed. And now that our production
volumes have increased, we also buy
more wood. We need an extra 800,000
cubic metres of wood per year,”
explains Laaksonen.
The pulpmill’s investments are
visible over an extensive area. The
increasing demand for wood has sped
up harvesting, which in turn brings
more money to forest owners. The
knock-on effects are extensive, not
only regionally, but also nationally.
Above all, the investment has had a
positive impact on the atmosphere
at work. “Pulp is valuedmore than
before, whichmeans manufacturing
is profitable. The modernised pulp
mill is an attractive workplace,” says
Mikko Pajari
, supervisor of the pulp
mill’s morning shift. After all, why
would anyone leave a job with solid
long-termprospects?
Modernised softwood fibre line
We leave the debarking plant and head
for the next improved site, the fibre
line. A traffic sign points us in the right
direction. We pass a huge white liquor
tank to reach the control room, where
we find several line operators closely
analysing complex charts on their
monitors. These charts tell themhow
much chlorine dioxide is being used,
for example. This is an issue that is
especially important to departmental
supervisor
Mika Hohti
. Apparently,
consumption has decreased, which
seems like good news.
plant. Normally the noisiest part of
the integratedmill site, the debarking
plant is silent today because of a
shutdown. There are no logs moving
down the production lines, of which
there are now two instead of just one.
The new line, which debarks and chips
birch wood, was built alongside the
old one in June.
Clad in overalls, debarking plant
manager
Markku Tamlander
and
plant worker
Jouni Martikainen
have just replaced the chipper’s
blades. How do they see the
investment as having impacted their
everyday work? “Manufacturing
is steadier now. There are fewer
production interruptions. And it’s
more cost-efficient,” Martikainen
says.
The chipper gets blocked less often,
for example. Another major benefit is
the fact that one of the lines remains
in use even if there are problems with
the other. “We have higher production
volumes and the end results are better
quality,” Tamlander says. And that,
indeed, is what everyone wants: better
products.
The quality assurance process in
fact begins far away from the mill, in
the forest, with the expert wood buyer
who selects the logs. They mustn’t be
too thin or rotten, and they mustn’t
be allowed to rot by keeping them on
the roadside or in a warehouse for too
long.
This must mean that the piles of
logs in the debarking plant’s yard will
Jouni Martikainen keeps a close watch
on the new debarking line.
Jouni Martikainen