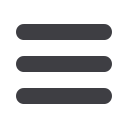

1/2016
|
49
Hohti lists some of the
improvements that have been achieved
thanks to the modernisation of the
softwood fibre line. “We replaced
the old atmospheric diffuser in the
brown pulp scrubber with a DD
scrubber. As a result, pulp-scrubbing
quality, runnability and capacity have
improved.”
Another improvement is that
branches are efficiently sorted and
separated, which reduces the amount
of rejects and impurities and improves
output. What this means in plain
English is that the mill gets more high-
quality pulp from a smaller amount of
wood. Bleacher
Aki Korpela
explains
the secrets of pulpmanufacture in
metaphoric terms: “We make rice
pudding out of barley porridge,” he
jokes laconically. In essence, he’s right:
when youmake pulp, you remove
the brown colour, or lignin. The final
result is a white, porous substance that
you can scrape out of the scrubbers,
which look like large baking ovens.
The difference between bleached and
unbleached pulp is obvious from the
two warm, wet, odourless samples we
are handed from the birch line: one is
brown and the other bright white.
In addition to the modernisation
of the fibre line, the third significant
improvement made at the plant concerns
energy efficiency, as explained by
operations manager
Matti Tikka
at
the chemical recovery plant.
“Our energy utilisation is more
efficient, and we are producing higher
volumes of heat and energy. The mill’s
self-sufficiency rate in terms of energy
production has increased to more than
85%,” Tikka says.
More heat is generated because more
black liquor is combusted in the recovery
boiler. The excess heat is sold to the
district heating network. The heat and
the ‘green electricity’ produced from
renewable rawmaterials support the
Group’s sustainability-based business.
There is only one final place to visit:
the drying machine. We walk another
short distance in the clear autumn air to
reach the most expensive investment,
which is located on the paper mill side,
on the site where paper machine no. 7
used to be before it was dismantled
years ago.
Efficient drying machine
This time we enter a control room that is
chock-full of bustling people. We watch
the monitors and see how the pulp sheets
move along the packaging line towards
Energy efficiency has improved
considerably. The mill self-generates
higher volumes of heat and electricity,
says Matti Tikka at the chemical
recovery plant.
Supervisor Mika Hohti monitors chlorine dioxide
consumption. Bleacher Aki Korpela is on the right.
robot claws. Bales ready for export are
neatly packaged with wrapping and
wire. Those without wrapping will be
transported within Finland.
There was a clear need for a new
drying machine, as the old one was
already more than 50 years old and is
currently being dismantled. “The pulp
mill can now operate at full capacity
even if the paper mill is at a standstill.
Production had to be slowed down
before, but nowwe are able to even
out the consumption,” explains
operating engineer
Jukka Flinkman
.
There are other benefits too: the
current machine efficiently cools
down the pulp web, which reduces
the yellowing tendency of the pulp,
which canmar the brightness of the
end result. The bales also look more
attractive now, which is important to
customers.
Our tour is nearing its end. We
pass from the control room to the
warehouse fromwhere the pulp is
sent to end customers to be processed
further. As steam rises from the water
in the wastewater treatment plant,
forklifts scurry about and trucks with
licence plates from several countries
are being loaded with brilliant white
pulp bales. A train carriage has just
been loaded: most of the pulp travels
to customers by train.
The autumn day draws to an end.
The evening shift takes over from the
morning shift. The pulp bubbles away,
and the paper machines roar. All is
well at the Kymi integratedmill site.
Matti Tikka
Mika Hohti, Aki Korpela