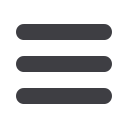

46
|
BIOFORE
P
ine, spruce and birch logs
are neatly stacked next to
the debarking plant, with a
couple of aspens completing
the set. Next stop for these logs can be
seen a little further away: a tall pile of
wood chips. Conveyor belts criss-cross
the area, taking the wood chips to the
next stages of the pulpmanufacturing
process: digesters and scrubbers.
Trucks wait for their loads at one
end of the mill area, while forklifts
carry neatly wrapped white pulp
bales from the warehouse. Some carry
the red label ‘UPMBetula’, others
the blue label ‘UPMConifer’. The
bales contain the rawmaterial for
packaging, speciality paper, magazine
A pulp mill is reborn
We take a tour of the newly
revamped Kymi pulp mill to
find out what’s new, bigger
and better. Has UPM’s
EUR 160 million investment
made a visible difference?
and fine paper manufacturers. Most
of the pulpmanufactured at the plant
has already been delivered to UPM’s
own paper mill, where two paper
machines turn it into fine paper.
We are in Kuusankoski in southeast
Finland, at the heart of the Kymi
pulp and paper mill. The 200-hectare
integratedmill site is like a town
within a town. The site has streets
with real names such as ‘Fibre
Avenue’, ‘Wood Chip Road’ and ‘Sheet
Street’. Odourless columns of white
steam rise into the blue sky from the
chimneys of the clean, orderly site.
Here, on the shores of the Kymi
River, overlooking miles of coniferous
forests, wood is turned into pulp and
“The new drying
machine does a
brilliant job”, says
shift supervisor
Mikko Pajari.
Mikko Pajari
TEXT
HELEN MOSTER
PHOTOGRAPHY
TUOMAS UUSHEIMO