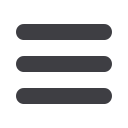

N
ovember
2009
125
›
Figure 3
:
An example forming roll flower of 12mm x 1.8mm
The example for 12mm x 1.8mm (outside diameter x thickness) tube
flower pattern is shown in Fig.3
2 Pre-processing of finite element modelling
(FEM)
2.1 Geometric modelling
The 3D finite element modelling used for ERW tube forming in this
example includes rolls and strip coil. The roll drawing is generated in
COPRA in AutoCAD format with extensions of DWG or DXF. Before
being imported into Marc, the roll drawings are simplified, leaving only
the outer contour line and axis, and deleting the other information.
For the symmetric rolls drawing, in order to reduce the time of
computing, only half of it is for simulation. The rolls DWG files
are converted into DXF (AutoCAD2000) format, then rolls outline
drawings are imported into Marc, and the rolls contour lines are
rotated around the shaft axis in Marc to form roll surface.
2.1.1 Idealising rollforming machine
In order to simplify the process of roll forming, assume that the roll
forming machine is ideal for the purpose intended: during numerical
simulation, assume rigidity of the roll forming machine is just enough
and do not consider deflection caused by the force applied on the
shaft. Also assume positioning of rolls to be correct, ignore errors
from installation and assume sheet material for forming is also ideal.
Finally, ignore thickness errors of coil.
2.1.2 Rolls are rigid bodies
Since rolls material is die tolling steel with little distortion during
forming, the rolls should be regarded as rigid bodies.
2.1.3 Relative motion equivalent
During actual production, the rolls rotate to drive sheet material
passing the roll-forming machine. According to the principle of
relative motion, it is equivalent to the rolls slide static sheet material.
Static sheet material is convenient for applying boundary conditions
and simplifies distortion analysis.
2.1.4 Ignore friction
The reasons: during forming, force of friction drives sheet material
forward, so there is little effect for forming. If friction is ignored,
computational complexity is obviously reduced, and the result is
easy convergence. In situations of small diameter thick-wall tube,
no obvious simulation analysis precision error is found by comparing
results considered friction and ignored friction.
2.1.5 Use a piece of sheet material to replace a whole coil of
sheet material
A whole coil of sheet material is used in actual production. In order
to reduce computational complexity, use a piece of sheet material
to simulate forming with a whole coil of sheet material. In order to
guarantee stable forming between passes, length of sheet material
for simulation should not be less than 1.5 times the distance
between passes. In order to avoid influence caused by errors at
start of work piece and end of sheet, the middle
1
/
3
part of simulation
sheet material is selected during analysis.
2.1.6 Partition of sheet material units
Since round tube is symmetric, only half of it is simulated. The
centre distance between adjacent two passes is 100mm, length of
sheet material is 150mm, and sheet width is calculated according
to various diameters and sheet thickness. Divide the forming body
into 20 equal parts horizontally (direction X), and three layers along
direction of thickness (direction Y), and 150 parts along the direction
of feeding (direction Z), total 9,000 units.
Figure 4
:
The co-ordinate used for modelling
The element type seven (an eight-node, isoparametric, arbitrary
hexahedral) is chosen. The equivalence simplifies and reduces
computational complexity of contacting search during the
computational process.
2.2 Definition of geometrical features
Since stress, strain and displacement changing of sheet material in
X, Y and Z directions during roll forming are considered normally, it
can be defined as a 3D problem. Here 3D solid units are adopted.
Because there is lack of shearing behaviour description, in order to
remedy it, the method of assumed strain is used. By using selected
interpolation to improve describing capacity of shearing (bending)
behaviour. Since volume of material before and after distortion is
constant, choose the item of constant dilatation.
2.3 Definition of material characteristics
During this simulation, sheet material is Q235 with Young’s Modulus
of 210Gpa, Poisson’s Ratio is 0.3.
2.4 Set boundary conditions
An important content during simulation modelling is definition of
boundary conditions. Fix longitudinal displacement of the sheet
first, apply direction Z fixed displacement at both the front and
rear of the sheet and try to avoid applying any constraint at the
node of distorting area. Since only half of symmetrical simulation is
analysed, apply lateral constraints on the symmetry axis. Direction
X displacement constraints. In addition, a single sheet with a certain
length is used during simulation, while it is coil continuous forming
during actual production, so apply proper constraints vertically to
prevent the swinging of work piece and sheet end. Apply certain
direction Y displacement constraints to avoid too large displacement
in vertical direction. During direction Y constraints applying, pay
attention to the positions, which must be nodes without vertical
displacement changing before and after forming.