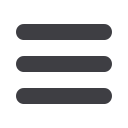

N
ovember
2009
127
›
North China University of Technology
– China
Fax: +86 10888 03581
Email:
fao@ncut.edu.cnWebsite:
www.ncut.edu.cn
Figure 10
:
Errors of welded
tubes with various ODs and
same wall thickness
The fitted equation of the curve is δ
D
=1.484-0.139 D +0.004 D
2
,
where δ
D
is the dependent variable roundness error, and D is the
independent variable outside diameter, the curve of δ
D
changing
along with D is the left half of a second-degree parabola.
3.4 Analysis of wall thickness changing
To investigate the symmetry of welded tubes, divide a half circle
of the welded tube into ten equal parts (Fig. 7), analyse thickness
changes, Fig. 11 is the
changing curve.
Figure 11
:
Wall thickness
changes on a half circle
of welded tubes in all
specifications
3.5 Comparing with other research
Figure 12
:
Relation between strip material thickness and perimeter position
German dataM company and Darmstadt University performed
simulation and experiments for 60mmx1.5mm ERW tube, and
obtained results as Fig. 12. The extreme values appear near the
axis of symmetry (0°), positions of sheet edge (180°) and close to
90°. The trend of the curve is similar with the result of simulation
here, which proves that the result of this simulation is authentic.
3.6 Methods for reducing wall thickness error
According to the wall thickness changing after forming (Fig. 11),
it is hard to meet the requirement of accurate forming if you only
depend on the roll flower to design the outer contour line of the rolls.
In order to reduce wall thickness error, it is necessary to modify roll
gap based on the former roll flower design, and decide the corrected
value according to wall thickness error in the diagram.
During forming, edge of sheet will form at the first bend, so
remedy the error of 115°-180° wall thickness at the first pass; and
distribute the error of 0°-115° wall thickness to all main roll passes
before fin pass. In this way, after the roll shape contour with error
compensation is formed, error of wall thickness may be easily
reduced to meet the requirement of high accuracy welded tubes with
uniform wall thickness.
4 Conclusions
1) With the same outside diameter, the roundness error clearly
increases along with wall thickness. By analysing the fitting
results of the curve, the polynomial equation for wall thickness
and roundness error is δ
t
=0.493-0.585 t +0.191 t
2
,.
2) When wall thickness is constant, roundness error reduces
and outside diameter increases. By analysing fitting results of
the curve, the polynomial equation for outside diameter and
roundness error is δ
D
=1.484-0.139 D+0.004 D
2
.
3) When the curve of wall thickness changes, total trend is
degressive. There are three larger values of sheet thickness
at the half circle, which have appeared near the axis of
symmetry (0°), positions of sheet edge (180°) and close to
90°. From the result, the three larger values are all produced
at the final pass, which shows that very large compressive
stress occurs on sheet edge. The various simulations result
in a larger changing range at the end of sheet, which are
caused by distortion at the end elements.
4) By conducting the above mentioned roundness error analysis
and the changing rule of wall thickness, it is necessary to
modify roll gap according to wall thickness errors distribution
during design in order to reach uniform wall thickness and
realise high accuracy thick-wall tube forming. The rolls
contour is not only a simple arc, but a spline curve fitted
according to wall thickness changing, thereby determining
the actual rolls contour curve.
Acknowledgements
Thanks to Mr Zhao, Yun, GM of Huzhou Weiyun Moulds Co Ltd and
Mr Zhou, Shijia, GM of Ningbo Huaguan Machine Manufacturing Co
Ltd for support and help during the investigation of the topic.
References
Albert Sedlmaier. Predicting The Properties of Welded Roll Formed Tubes for
Subsequent Processes Using the Finite Element Method[C]. Valley. Germany.
George T Halmos, Roll Forming Handbook, Taylor & Francis, 2005.
H Ona, Jiying Liu, Roll Forming Technology, Chemical Industry Press, Beijing 2007.