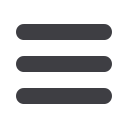

J
anuary
2009
www.read-tpt.com68
›
S
traightening
and
finishing are critical
functions of tube
making on two counts: as
important contributors to the
quality of the product; and by
virtue of their position in the
production cycle.
In a high-speed operation,
problems are unwelcome
at any time. In an industry
in which profit turns on
productivity, they are best
discovered at the feedstock
stage.
As it happens, there are
challenges enough at the
end of the line. Expectations
for
finishing
grow
continually, especially in the
pharmaceutical and chemical
processing industries that require a mirror finish on the interior of tubing.
It is no longer sufficient for tube finishing methods to deliver a smooth, blemish-free surface
with a high-gloss polish; they must also satisfy stringent government-mandated health, safety,
and environmental concerns. Operations such as buffing may now require the installation
of operator safety devices. Harder-to-grind metals call for customized polishing sequences
and belt lineups. Polishing the inside
diameter of very long tubes is still a
daunting assignment.
As their customers’ requirements
mount, so do the demands that tube
makers place on themselves: for
achieving perfect surfaces in fewer steps
and in less time. The development of
new machinery – for straightening,
grinding, sanding, and polishing –
keeps pace with both sets of clients.
Bronx/Taylor-Wilson manufactures a range of 6 and 10 roll straightening machines (see page 72)
S
traightening &
F
inishing
M
achinery
Ravni technology for a prime finish on steel, copper and stainless steel tube (page 80)