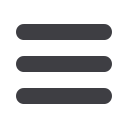

J
anuary
2009
www.read-tpt.com70
›
S
traightening &
F
inishing
M
achinery
reached, the method of deburring
with high performance brushes is
well-established. The necessity of a
perfect quality and highest assembly
simplification do not permit deburring
methods that are dependent on the
qualification of the operator.
RSA has developed different fully automatic
deburring systems, especially for high
quantities. However, there is much potential
for rationalization in this area, with improved
interlinking of different working steps. The
direct interlinking of deburring systems with
preceding saws from other suppliers, or the
interlinking of cleaning modules, can lead to
lower processing times.
RSA GmbH & Co KG
– Germany
Fax
: +49 2351 995 300
:
tiemo.krause@rsa.deWebsite
:
www.rsa.deRSA Ltd
– UK
Fax
: +44 1952 580511
:
rsa.gb@rsa.demakes a second rotation: it turns on its own
axis. This second rotation assures complete
deburring of the tube and section edges
without having to turn the workpiece manually.
According to the agricultural machine
manufacturer, the advantages of the
system are the reproducibility of deburring
results, simpler handling for the operator,
and a drastic reduction of the deburring
costs. It is possible to reduce the deburring
time per end face from 30 to 4 seconds.
Based on the daily production of about 700
workpieces, the amortization period for the
machine was less than 2 months.
In many areas of pre-production,
especially within the automotive supply
industry, where high quantities are
RSA GmbH & Co KG, Germany, is a
specialist in cutting and deburring systems
for tube and pipe manufacturers. The
company has recently supplied a Turnamat
deburring system to a manufacturer of
agricultural machines that uses hydraulic
tube products.
During pre-production of hydraulic tubes,
the company had previously used a
file to remove outside burrs and a spot
facer to remove inside burrs. However,
the company now uses the Turnamat
deburring system to carry out these
procedures with far more efficiency.
Using this machine, a high performance brush
operates as a tool. In addition to the rotating
movement, the high performance brush
Advanced deburring systems enable
higher productivity
The Turnamat deburring system is suitable for unwieldy workpieces such as bent tubes. Inside and outside
burrs are removed reliably in one work process without having to turn the workpiece manually
The deburring principle: in addition to the rotation
of the brush, the workpiece turns on its own axis.
Normally, the deburring time is about 3 seconds
also in case of complex workpieces
belts, deburring wheels and similar
methods.
Changeovers are easy and can be
completed within minutes with four sets of
tools covering a
5
/
16
" to 2" diameter range.
Eight spindle speeds are available from
760 to 3,920 RPM and the maximum stroke
is 1
1
/
4
". These end-finishing machines are
easy to operate and come with a variety of
accessory equipment and tooling options.
Manchester Tool & Die Inc
– USA
Fax
: +1 260 982 4575
:
edegner@manchestertoolanddie.comWebsite
:
www.manchestertoolanddie.comrod end-finishing machines for fast and
simultaneous deburring, ID/OD chamfering,
and facing.
Model 660 includes two models, a manually
operated and an air operated machine, for
finishing up to 1,500 ends per hour and
1,875 ends per hour respectively.
These end-finishing machines offer
cost savings by freeing lathes and other
machines on a wide range of work. Model
660 can also increase production and
improve accuracy compared to abrasive
Manchester Tool & Die Inc, USA, now
offers the Pines model 660 tube and
New tube and rod end-finishing machine
The model 660 tube end-finishing machines