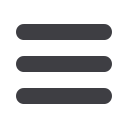

69
J
anuary
2009
www.read-tpt.com›
S
traightening &
F
inishing
M
achinery
As the outside diameter of tube gets
increasingly smaller, the difficulty in
rotary straightening slowly increases.
Historically, tubes with outside diameters
below 0.080" (2mm) have been extremely
difficult to straighten on rotary straightening
machines.
Tubes less than 0.60" (1.5mm) have been
straightened on manually operated devices
including a device commonly known as a
‘whizzer’. All such devices have never really
been controllable and at best produced
inconsistent tube straightness.
Over the years, other machinery designers
have made unsuccessful attempts at
designing a conventional rotary tube
straightener to handle tubes down to 0.040"
(1mm) tube OD. Makers of stainless steel
tubing used in the medical industries have
been searching for a machine to precision
straighten very small and thin wall tube for
many years.
Turner, USA, has long been known for the
design and manufacture of straightening
machinery that includes a unique approach
or feature. For a number of years Turner
has continually reviewed the possibility of
adding a miniature precision straightener
to its range. In 2005/2006 Turner
engineered improvements to two small tube
diameter straightening machines made by
competitors, which resulted in a definitive
improvement in their capability.
In late 2006, a respected company
approached Turner and requested the
consideration of the development of a
precision straightener to handle high
yield, thin wall stainless steel tube
down to 0.040" OD. A decision was
finally made to proceed with a project
to design and develop a fully computer
controlled miniature 10 roll precision
rotary straightening machine. As a result,
the company launched the Turner model
911.25 10 roll Casam I machine with
digital tube pressure sensing system.
Following development of the machine,
components were tested and software
engineers established Casam software
(computer aided setting and management).
This software advanced the resolution
of the system by a factor of 10 to enable
very small roll position changes and allow
monitoring and recording of the pressure
applied.
The finished model 911.25 machine was
powered up in January 2008 and undertook
its first trials. The ability to set roll positions
with extreme precision was proven within
the first day or two of machine testing.
The measurement of the pressure being
applied by each pair of rolls with digital tube
precision was more accurate than had been
expected. It proved to be totally necessary
to control the tube as it was threaded up
and run through the machine.
The Turner auto-acceleration drive system
enables very accurate and easy tube
thread-up into the 5 pairs of machine rolls.
It also enables the ejection of the tube end
from the machine at the end of the fully
automatic straightening cycle.
The machine is configured with 5 pairs of
driven rolls. As per common practice, the
rolls can be adjusted in height and angle
to enable tubes of different diameters to be
accommodated.
The roll to tube pressure sensing is
accomplished by strain gauges fitted
into the base of the machine. Extremely
accurate roll RPM’s are achieved by two
AC vector drives with unique control that
ensures the tube is maintained on the
centreline of the machine.
The new model 911.25 10 roll Casam I
precision straightening machine is capable
of straightening tubes from 0.040" (1mm)
up to 0.100" (2.5mm).
Turner Machine Company Inc
– USA
Fax
: +1 330 332 5871
:
rpage@turnermachineco.comWebsite
:
www.turnermachineco.com‘World’s smallest’
computer driven precision tube
straightening machine
Turner has developed the model 911.25 tube straightening machine