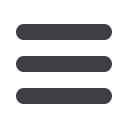

110
N
ovember
2013
Welding technology
Keyhole TIG redefines tube
and pipe welding
AUSTRALIAN welding innovator K-TIG
is now in full production of its game-
changing keyhole TIG welding solution,
and is focusing predominantly on the
tube and pipe welding market.
The Adelaide-based company, whose
K-TIG welding system performs welds
up to 100x the speed of traditional
TIG welding, has completed extensive
product trials in seven countries and
is now shipping its keenly awaited
first production units to customers in
Australia and worldwide.
K-TIG’s first export sales have been
to the UK, Middle East, China and India
where K-TIG’s distributors are focused
on the tube and pipe, oil and gas and
other markets.
K-TIG has recently appointed Sydney-
based Innovative Welding to spearhead
its Australian distribution.
“We are absolutely delighted to be
representing K-TIG in Australia,” said
Adam Poole, general manager of
Innovative Welding. “The reception to
this autogenous technology has been
tremendous, and productivity benefits
are shaping up to be enormous. It
already appears to be set to become the
de facto standard for circumferential and
longitudinal pipe welding,” he said.
The new welding technology, originally
developed by the CSIRO before being
acquired by K-TIG, enables thick gauge
materials, including traditionally difficult
metals such as stainless steel and
titanium, to be welded in a fraction of
the time possible with standard welding
processes.
K-TIG CEO Neil Le Quesne said
“K-TIG’s technology is transformational,
and likely to be highly disruptive within
the welding equipment market. The
lightning speed of the welding process
and, in many cases, a 95 per cent
reduction in power and gas consumption
dramatically reduces both the cost and
carbon footprint of industrial welding.”
“Due to the single-pass, full-
penentration nature of the process, the
weld quality tends to excite the head
of engineering, the enormous cost
savings get the attention of the CFOs
while the massive reduction in energy
consumption tends to get interest from
CEOs,” said Mr Le Quesne.
“The opportunities within
the tube and pipe sector
are enormous. There are
100,000 kilometres of new
pipeline currently in the
planning or construction
phase around the world,”
said Mr Le Quesne.
As well as offering huge
benefits to the tube and pipe
industry through time saving,
reduced energy costs and
lower reliance upon highly
skilled labour, the K-TIG
system is cloud-enabled
and records comprehensive
weld data for audit and
control purposes.
The recording and auditing
capabilities of the system
are considered vital to tube
and pipe sector, where
traceability is now becoming
a critical issue.
K-TIG founder and R&D
manager Dr Laurie Jarvis
led the 20-person CSIRO
team who developed the
underlying technology.
“Creating and stabilising a keyhole
in molten metal using TIG welding was
previously not thought possible,” says
Dr Jarvis.
Fully understanding the physics
involved and developing techniques to
fully control the process took Dr Jarvis
and his team more than eight years. “We
ultimately developed the tools and high
speed processing capability required
to deliver an extremely robust welding
process which is up to 100x faster
than TIG, uses up to 95% less power,
up to 95% less gas, requires no edge
preparation and allows high-speed,
full-penetration, single-pass welds to
be performed by individuals with no
welding experience.”
“The K-TIG process excels with
materials that are traditionally very
challenging to weld,” he said.
“Stainless steels, titanium, zirconioum,
nickel alloys, cobalt alloys and others are
welded to nuclear industry standards in
a fraction of the time taken by traditional
TIG welding.”
“Take a 16mm titanium steel pipe,”
said Dr Jarvis. “When welded using TIG,
you would need to prepare the edges of
the material into a V profile, you would
need to perform the weld in 12 separate
passes, and for every metre travelled
you would have an arc-on time of 156
minutes, consume 665 grams of filler
wire, 5,000 litres of gas, and the weld
would need to be performed by a highly
skilled welder,” he said.
“When welded with K-TIG, the same
weld requires no edge preparation, no
filler material, no skilled welder, and
for every metre travelled you have
arc-on time of just 4 minutes, and gas
consumption of just 240 litres of gas.”
“The K-TIG process is ideally suited
to both longitudinal welds which run
along the length of the pipe, and
circumferential welds which join pieces
of pipe end-to-end. The next stage of
development is a 5G variant of the K-TIG
system which will be clamped to a track
on the exterior surface of a pipeline in
the field to automate pipeline welding,”
said Dr Jarvis.
K-TIG
– Australia
Email:
neil.lequesne@k-tig.comWebsite:
www.k-tig.comThe K-TIG welding system