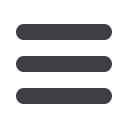

Welding technology
www.read-tpt.com112
N
ovember
2013
Weld engineering supports
oil and gas projects
HIGHLY specialised welding and com-
plementary
services
such
as
fabrication,
machining,
corrosion
protection and NDT in the oil and
gas sector are available to meet the
diverse needs of equipment suppliers
manufacturing a range of components
from pipelines and flanges to risers and
pigging systems.
However, finding all, or even a few,
of these disciplines from a single-
source supplier is rare as the need for
an in-depth understanding of so many
disciplines, and their equally wide and
demanding quality standards, requires
vast knowledge and experience.
Gloucestershire, UK-based weld
overlay cladding and fabrication
specialist Arc Energy Resources has
successfully completed many projects
that required such a multi-disciplined
approach.
Commenting on the multi-disciplined
approachtoitsweldingservice,managing
director Alan Robinson stresses the
company’s significant investment in
training and its commitment to meeting
worldwide certifications and industry
standards. Whatever a customer
needs, from design for manufacture to
final NDT, Arc Energy has the industry
standard resource to exceed its clients’
expectations.
In addition, Arc Energy holds ASME U
and National Board R Stamps, enabling
the company to provide code compliant
pressure vessels and subcontract
welding on free-issue ASME standard
material.
These accreditations are part of Arc
Energy’s list of qualifications, which
also include ISO 9001:2008 quality
management system, ISO 14001:2004
environment management system,
Investors in People, and OHSAS 18001
health and safety management system.
Arc Energy also remains one of the
few welding specialists that can boast
accreditation to the ISO 3834-2 welding
quality standard and conformance to
ISO 14731, Welding Coordination.
If size and tight tolerances require
stress relieving after weld overlay
cladding, even with large items of
equipment, Arc Energy is able to carry
out post-weld heat treatment in one of
its own calibrated furnaces.
Add to that the fact that Alan Robinson
is himself one of very few UK registered
International Welding Engineers, has
a Masters degree in welding, and is
a Chartered Engineer, a European
Engineer and a senior member of the
Welding Institute. All of this reinforces
the fact that few welding specialists
can equal this list of accreditations,
or provide Arc Energy’s capability to
support clients with a multi-disciplined
welding, fabricating and engineering
service delivered by highly qualified and
experienced welding staff.
Arc Energy Resources
– UK
Fax: +44 1453 823623
Email:
sales@arcenergy.co.ukWebsite:
www.arcenergy.co.ukArc’s cladding station
Launch of Argweld pipe weld
purging systems
HAVING been manufacturing tube and
pipe weld purging systems since 1975
Huntingdon Fusion Techniques HFT
®
has evolved the science of weld purging
to new levels.
The company has now reached the
fifth version of its tube and pipe weld
purge system designs by launching
the new PurgElite
®
range systems
for diameters from 1" to 24" diameter
inclusive.
These systems are suitable for all
industries using tubes and pipes.
In particular, PurgElite
®
systems can be
used in high quality tube and pipework
where the internal surfaces may be
polished to ensure minimum entrapment
and low corrosion resistance. With the
new Intacal
®
specially designed in line
purge valve and the synthetic hose
protection, there are no metal parts to
scratch the tube or pipe surfaces.
IntaCal
®
needsnosettingor controlling,
but is precisely manufactured for the
PurgElite
®
method of weld purging.
This new range comprises 15 models
for tube and pipe sizes from just under 1"
to 24", each one overlapping the range
of the other so that all internal diameters
from 20 to 610mm are covered.
The new series has a number of major
advantages over previous weld purging
systems and has taken into account the
evolving technology in all market places
where much higher specifications of
materials and work finish are available
and expected.
PurgeGate™ is a worldwide patented
device fitted to the front of each inflatable
purge system to protect it from bursting.
No matter how high operators turn up
the pressure, it is impossible to cause
the purge system to burst due to over
pressurisation. A benefit to this device
is that the flow rate may be increased
as desired without damage to the weld
purge system.
Huntingdon Fusion Techniques Ltd
– UK
Website:
www.huntingdonfusion.com