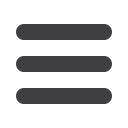

Technology News
www.read-tpt.com72
N
ovember
2012
Scanners with diameter control
ZUMBACH Electronic, Switzerland,
has extended its range of ODAC
®
laser
scanners for non-contact inline diameter
measurement for large size solutions.
With the ODAC 550 it is now possible
to measure large steel bars, tubes and
rolls up to 500mm or more at accuracies
of a few metric microns and rates of
up to 2,000 measurements/s. Other
materials, such as titanium, brass, alloys
and plastic, work as well.
This was made possible by the
development of a revolutionary optical
scanning technique with a highly
parallel and seamless measuring field
(no dead zone). The technology also
allows mounting emitter and receiver
far apart from each other, depending on
the available space conditions. Typical
processes where the system offers new
solutions are peeling, grinding, polishing
and straightening, as well as in quality
control lines (NDT).
The dimensional data for diameter,
ovality, etc, can be fed directly to the
user’s network or displayed in real-time
for the operator by USYS processors,
and also for feedback to the machine.
Complete accessories like secondary
protection enclosures, cooling devices,
air purging and air knives are available.
Zumbach Electronic AG
– Switzerland
Website:
www.zumbach.comODAC 550
installed on the
biggest peeling
machine in the
world
Fast phased array system
FAAST II is a UT phased array system
especially designed for high speed
testing applications and production
lines, and able to replace more than
ten conventional phased array systems
working in parallel.
The system’s patented linear
pulsing generator allows multi-beams
transmission in one single shot through
out 1D linear multi-element probe, but
over all through out 2D matrix probes.
As an example, the first industrial
application being built by Socomate
using this method is an ultrasonic rail
testing car providing in-track inspection
at a speed of 100km/h with only one 1D
multi-element probe.
The most important industrial
applications are tube and pipe testing in
high speed production lines from which
FAAST II is able to detect and process
in real time all oriented reflectors in one
shot with 2D matrix array probes: pipe
longitudinal, transversal and all oblique
notches every 5° step over the 360°
circumference of tube, internal and
external, with lamination and WT at up
to 2.5m/s surface speed with 2D active
matrix or circular array probes; high
precision tube Ø10-60mm longitudinal
and transversal notches, internal and
external, at 24m/min linear feeding
speed with 2D active surrounding array
probes.
The FAAST II system is compatible
with any type of standard multi-element
probes as well as with active probes
embedding Socomate International
electronics with pulser, preamp and
multiplexer, allowing the limitation of
connectors when using a huge number
of elements as with 2D matrix array
probe 128x8 elements and only 64
connectors.
FAAST II systems with 2D active
surrounding probes for L&T flaw
detection, associated to the E.Rota-12
patented system for full dimensional
measurement (OD, WT, ECC, ID and
OV) are now available as a unique
option to rotary heads on linear feeding
high precision tube lines, and with no
mechanical rotating movement for
easy and quick probe positioning and
calibration, and reduced maintenance
costs.
Socomate International
– France
Email:
serge.c@socomate.frWebsite:
www.socomate.comLine polishing for tubes
THE latest evolution of PLS in-line
planetary polishing systems is a
completely reengineeredset ofmachines
providing improved performance and
compact design.
The PLS series now consists of three
machines with different dimensions
and output, which can be installed into
any existing or new production line for
tubes or bars. It is typical to find these
in stainless tubes mills, seamless pipe
production lines, bar drawing lines and
before NDT test lines to clean products
and improve reliability of the control.
The integration of PLS systems into
a line avoids additional handling and
allows both cosmetic polishing and an
important reduction of roughness, on
100 per cent of the production, and with
low running costs.
The most popular model is the
medium machine, PLS 600, which
features compact dimensions and can
also work on shorter products. The
covered workable range is from 6 to
104mm diameter, or from 20 to 220mm
diameter.
Surface Engineering Srl
– Italy
Website:
www.surfaceengineering.it