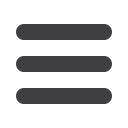

Technology News
www.read-tpt.com70
N
ovember
2012
Automated orbital welding
systems streamline in-process
inspections
by John Glessman, manager, welding
system products, Swagelok Company
PASSING in-process inspections for
orbital welding projects is critical, as a
failure can lead to costly rework, project
delays and system downtime. Today’s
orbital welding systems employ a variety
of automated features that help welders
complete more accurate, high-quality
welds and increase their likelihood of
passing in-process inspections. Even
more importantly, automation also
provides efficiencies for welders and
inspectors when conducting those
inspections.
Today’s orbital welding power supplies
automatically record the majority of
required welding data for projects.
Automated electronic data collection
ensures that searchable quality
assurance data is available to
welders and inspectors so each
party can conduct in-process
inspections in an efficient
manner.
Welders are typically required
to maintain comprehensive
data about each weld in a
project – a cumbersome
process that can account
for 30 per cent of total
construction labour hours
when performed manually.
Automated data collection
captures all of this data
with minimal operator input,
allowing welders to focus
on the welds. To ensure
complete data collection,
some orbital welding power supplies
highlight required data fields and do not
permit welding to start until operators
fill in all open fields. In addition,
welders can provide documentation
data electronically to quality control
administrators. Proper data transfer
yields a higher probability of passing in-
process inspections.
Electronic documentation data made
available to third-party inspectors
expedites their in-process inspections.
In an electronic format this data is
sortable and searchable, providing
inspectors with valuable efficiency
during their reviews. Electronic
documentation records also help
inspectors locate data faster compared
to leafing through hard copy weld logs.
This efficiency is especially helpful
given the varying documentation and
in-process inspection requirements set
forth by industries, applications and
owner companies.
For example, the biopharmaceutical
industry typically requires visual
examination of every weld. Welders
must visually check the outside diameter
of welds and record this information –
sometimes along with a video or image
file. With welds chosen randomly for
examination, inspectors can quickly
search electronic records to locate
specific welds and their data.
If a weld fails a test, the inspector may
search the electronic database to find all
welds performed during the same period
and review their parameters. Next,
the inspector may perform additional
testing on those welds and potentially
recommend rebuilding that portion of a
system.
Some power supplies present detailed
live weld progress data to help operators
better evaluate welds. Graphics show
the progression, performance levels
and stop/start for each level of a weld
in real-time. If the weld deviates from
the selected schedule, the graphic will
indicate points where those variations
occurred so the operator can evaluate
the weld after completion. This feature
enables welders to make efficient
adjustments to improve weld quality.
By leveraging automated orbital
welding power supply features,
welders enhance their ability to create
accurate, high-quality welds, while also
improving their efficiency in collecting
documentation
data.
Ultimately,
these automated features improve
the likelihood of passing in-process
inspections and creating leak tight final
systems.
Swagelok Company
– USA
Email:
john.glessman@swagelok.comWebsite:
www.swagelok.com
Orbital welding power supplies employ a variety of
automated features to help improve the quality of welds